This Austin-Healey 3000 MkII had been abandoned to a muddy grave. It took a mountain of effort, skill and money to make it perfect again
Words John Simister Photography Laurens Parsons
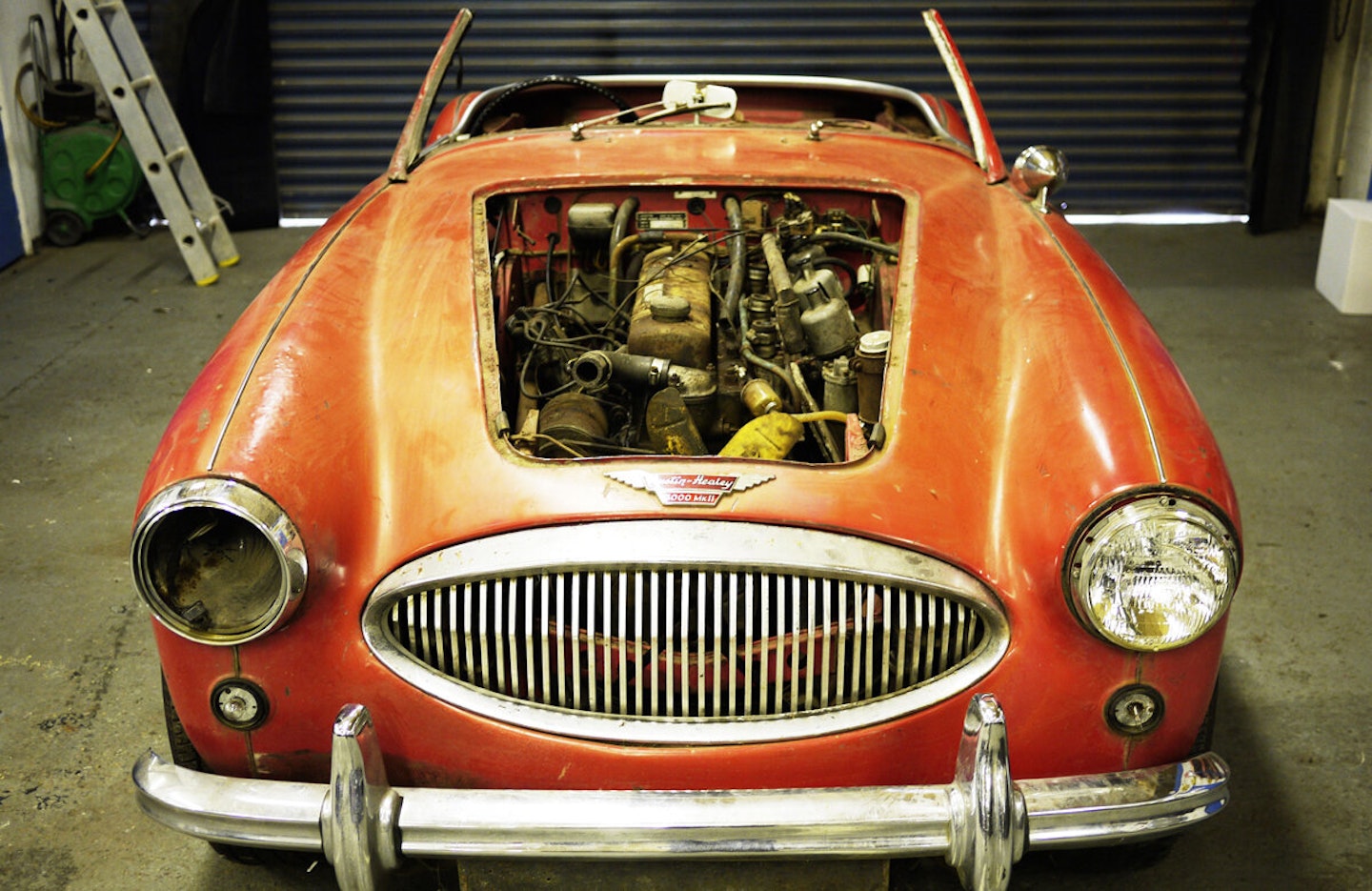
The fellow who took his part-dismantled Austin-Healey 3000 to JME Healeys around 1990 would kick himself if he could see it now. Trouble is, company founder Jon Everard never heard from the man again and the ’Healey just sat outside JME’s former Leamington Spa workshop under a tarpaulin, slowly sinking into a sloping grass bank surrounded by stacks of similarly dead cars and bodyshells.
Left to its own devices, the 1962 3000 MkII BT7 with triple SU HS4 carburettors would surely have returned to nature. But it was too complete a car and too nicely unmolested to deserve that fate, so after 17 years Jon checked out its ownership status, given that all attempts to contact its former keeper had drawn a blank. The legal view was that the ’Healey had by now become Jon’s. That will do nicely as a retirement project one day, he thought. Besides which, by then it owed around £30,000 in rent…
Dan Everard, Jon’s younger son, takes up the story: ‘We tried to move it, but when we tried to jack it up the jack went straight through the front crossmember.’ Blame years of mud and damp for that. Older son Chris (pictured above) continues: ‘It was in a bit of a sorry state. The front brakes had stuck on and we couldn’t unseize them. We eventually managed to get it on to castor wheels and drag it off the bank with a winch and into a container. Then dad built racking all around it and there it stayed for a few more years.’
“We tried to jack it up but the jack went straight through the front crossmember”
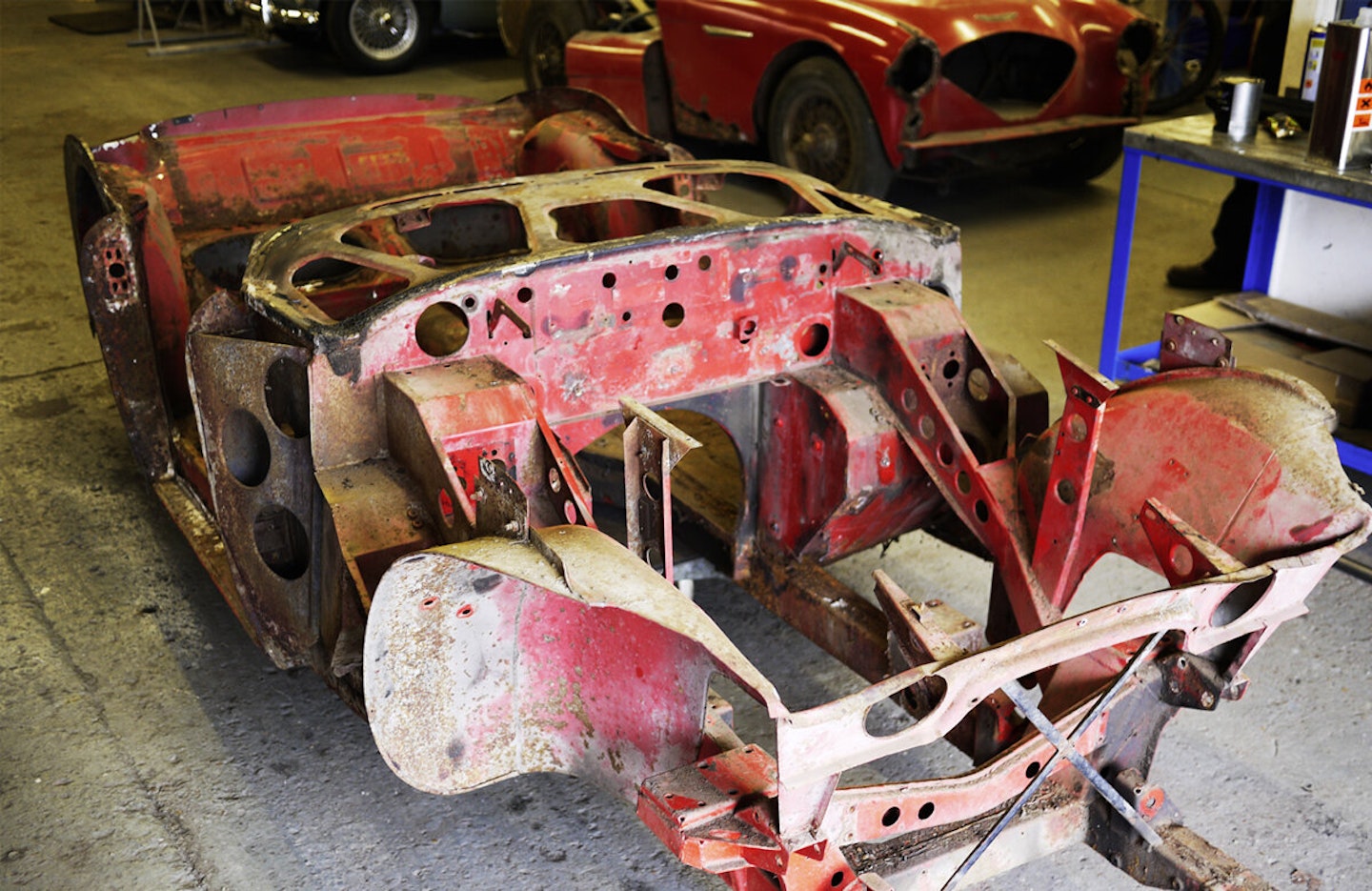
Each month Classic Cars magazine is packed full of great cars from the past, with inspirational human stories of pursuing, owning, driving, restoring and living with them; plus the latest and sharpest coverage of market trends, buying advice, events and news to help enthusiasts enjoy their classic motoring to the full.
Unfortunately, Jon, who served his apprenticeship at the Donald Healey Motor Company and knew the cars like almost no-one else, never did get to start work on the ’Healey. He died – too young – in 2010. By then his sons had been spending more and more time in the business, ‘Our parents wanted us to have lives of our own, but we’ve been immersed in it all our lives.’ So they took a leap into the future and pledged to keep JME Healeys as the mecca for ’Healey restoration it has been since 1978.
Thirty years after JME was founded one of the former Healey factory buildings in The Cape, Warwick (by then a carpet warehouse) became available. Here the ’Healey 100S models had been built, and later it was the special tuning department. Clearly JME Healeys needed to relocate to the most appropriate building there could possibly be, and it happened just before Jon so sadly died.
Chris and Dan decided the thing to do would be to take on the restoration their father never had a chance to start, so they dragged the 3000 back out of the container and transported it to the new workshop. That was 18 months ago, and now the ’Healey is finished.
‘We did it between other jobs,’ says Chris. ‘Normally we’d do a customer’s car in six to eight months.’
Which, when you read what chassis number HBT7L/18164 needed to get from sunk-in-a-bank to ’Healey-shaped perfection, would have been quite an impressive feat.
“We wanted to use as many original parts as possible”
CHASSIS AND BODY
Does the ’Healey have a separate chassis? It’s a semantic point. The chassis can exist on its own as a functional, structural unit, but the body is welded to it – and once that’s done it’s effectively a unibody with stout chassis rails. But whichever way you look at it the inner panels of ‘VSU 901’ were pretty rotten. The bonnet was missing, but all the other panels were present and most were original – a big bonus, reckons Chris, ‘If you can work with a car’s original panels, it goes together really well.’ One unoriginal part was a right-hand drive dashboard fitted as the start of a drive-side conversion shortly after this US-market car arrived back home in 1989. The Everards decided to reinstate the original left-hand drive configuration.
So the stripdown began of a car which looked, from a distance, a whole lot better than it was. The outer panels were all delicately soda-blasted. That meant drilling or grinding off some of the fixing bolts, but the hardest part was prising off the front shroud where it was stuck to the skeletal steel scuttle panel with mastic.
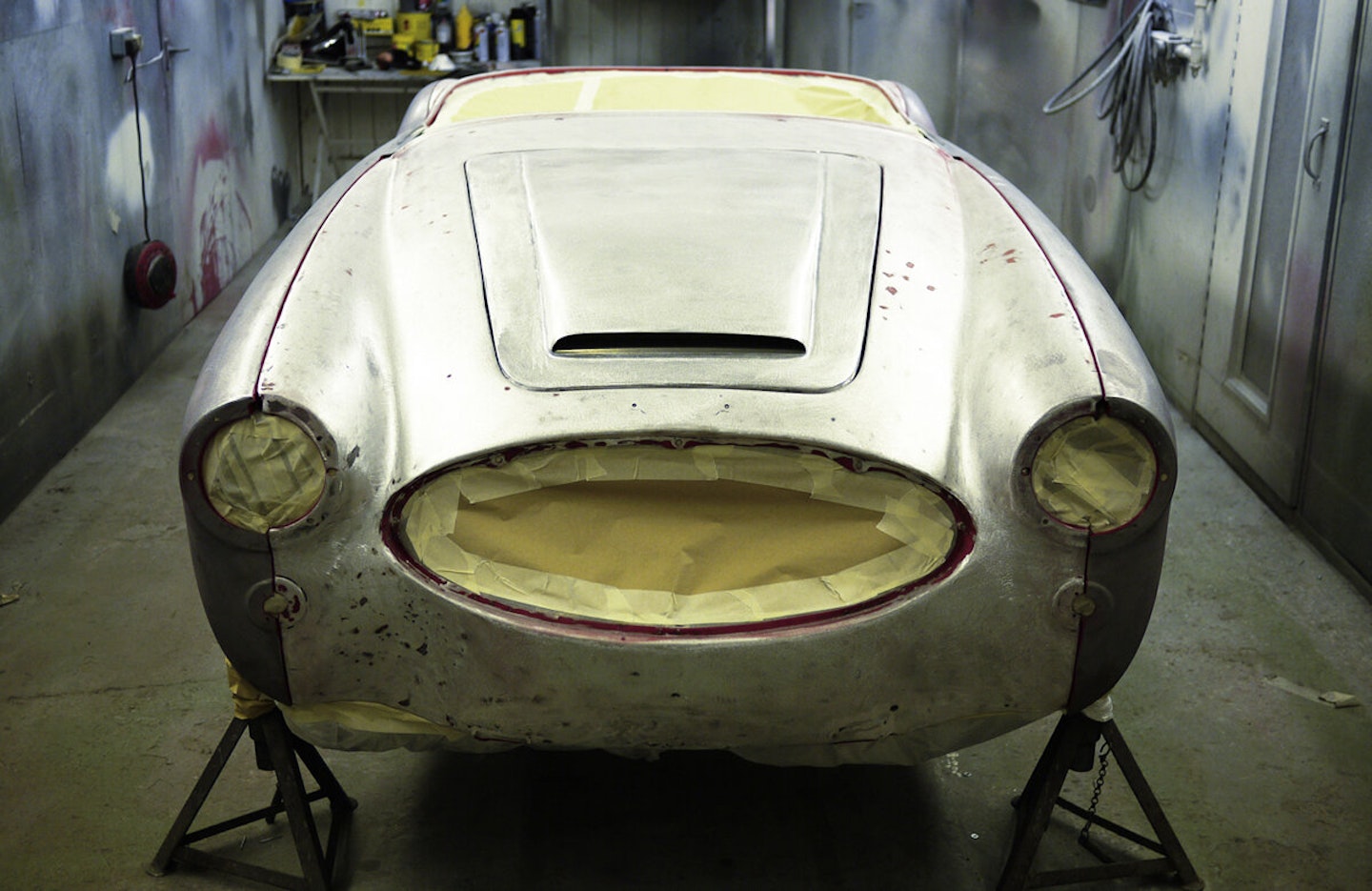
The stripdown confirmed the extent of the underside rot. The floors and footwells were holed, as were the fronts of the inner sills, the boot floor, and the boot ‘boxes’ with attachments for the rear leaf springs. JME replaced all these plus the inner and outer sills and the A- and B-pillars. ‘If more than a few inches are missing I put in a new panel,’ says welding maestro Dan Everard (pictured above). The front wings were deemed fit for re-use, as was the front valance, but the door bottoms and the lower sections of the rear wings were for the chop. ‘Dave Hardwick in Leicestershire makes panels for us and they’re absolutely superb.’
With all the panels removed, rusted sections cut away and mechanicals stripped out, all that remained was the chassis with its two bulkheads left attached to maintain their alignment, the front one with a jagged hole on each inner side panel where speakers had been crudely installed. Sandblasting followed. It was a chassis worth using, ‘Other restorers might say you’d need a new chassis,’ says Chris, ‘but do you really? The chassis is the birth of the car, and having the original one adds to its value. And in this car, especially, we wanted to use as many original parts as possible.’
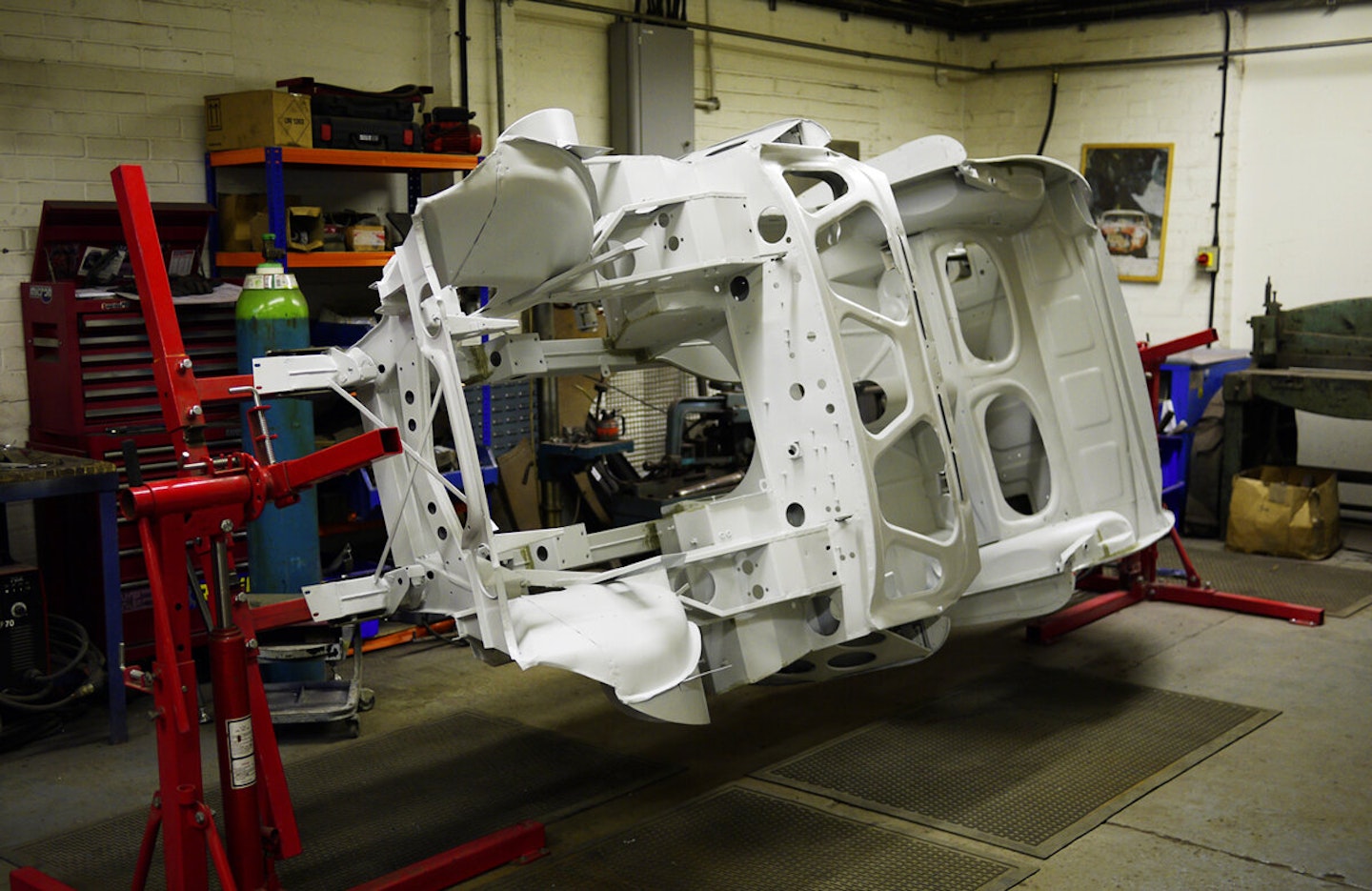
Dan set to work on the inner structure, replicating the stitch welds between new floors and chassis rails, invisibly welding steel into the speaker holes and replacing the front crossmember. As the welded outer panels went on, Dan seam-sealed where Austin-Healey never bothered: sills, pillars, even the rolled edges of the inner and outer wheelarches. That should keep the water out. A new bonnet came from AH Spares. The chassis got its paint and mechanicals, then panels were trial-fitted and adjusted for perfect gaps. When refitted they will ‘just click into place’, says Dan. Next, paint.
EXPERT TIP
‘It’s best to mount the body back on the chassis after you’ve done all the mechanical work and refitted the components,’ Chris advises. ‘It allows the chassis to settle first, which can affect the door gaps.’
“The car was all-red but the white flanks look fabulous”
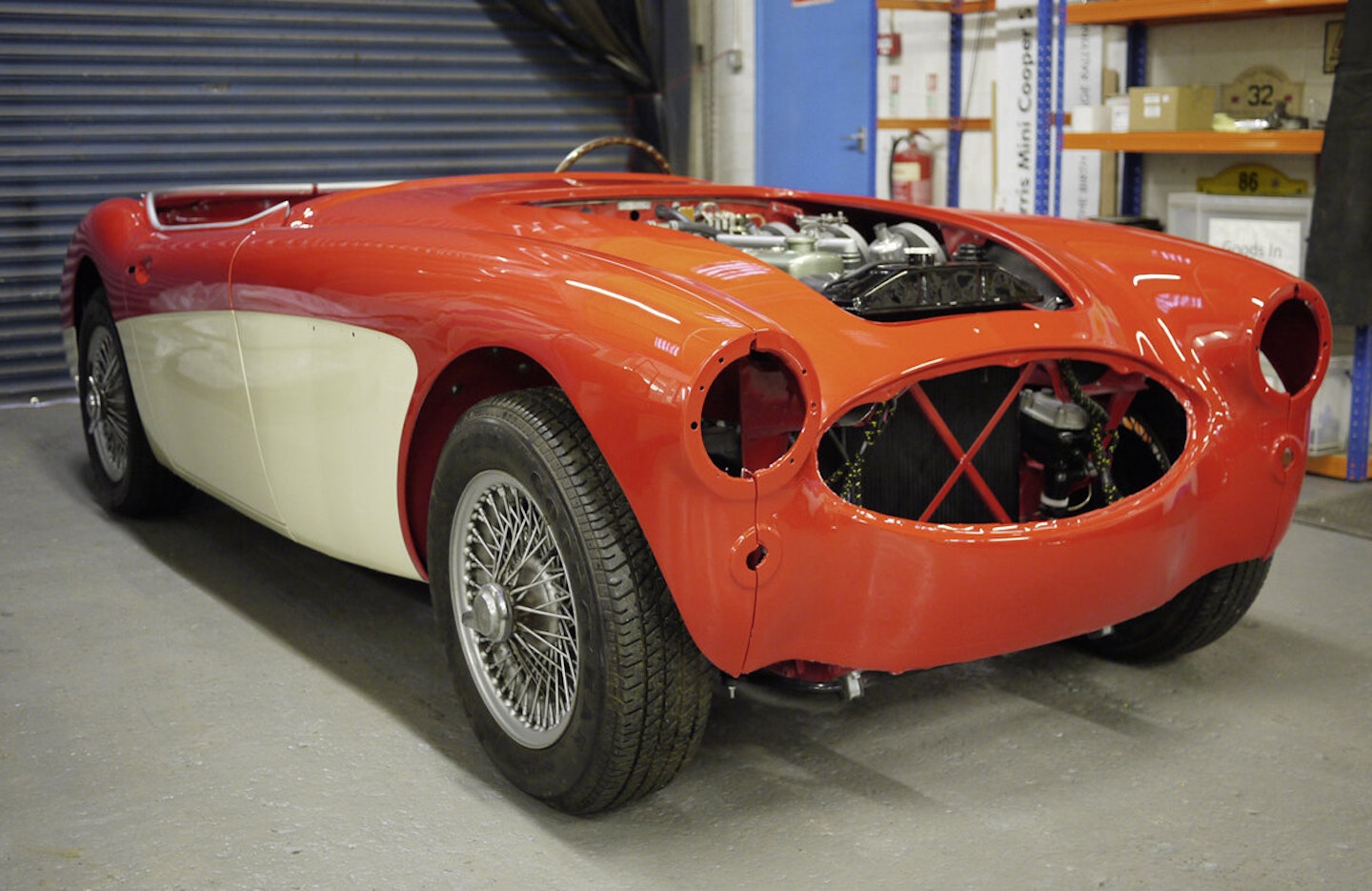
PAINTWORK
Paul Robbins – he’s been with JME since 1984 – first gives the rebuilt body and chassis a coat of Rustoleum, a tough coating used on oil rigs. ‘Even a sandblaster won’t take it off,’ says Chris. Next, Paul paints the chassis and inner structure in the main body colour. This done, the Healey’s hidden bits can be built up and the body tried for size. Only then can the body be painted.
Paul begins with three coats of very high-build polyester primer-filler. ‘I’ll probably sand two coats off, but it helps get all the swage lines and gaps perfect. Next come three coats of high-build primer, followed by a light guide coat. That’s sanded down, stopper used on any pinholes or scratches, then it’s re-primed.’
Next come three more coats of Colorado Red direct-gloss two-pack, after which Paul searches for imperfections and finds none. ‘Then I sand it with wet-and-dry until it’s matt, apply three more coats and sand again using finer and finer paper up to P2000 grit.’
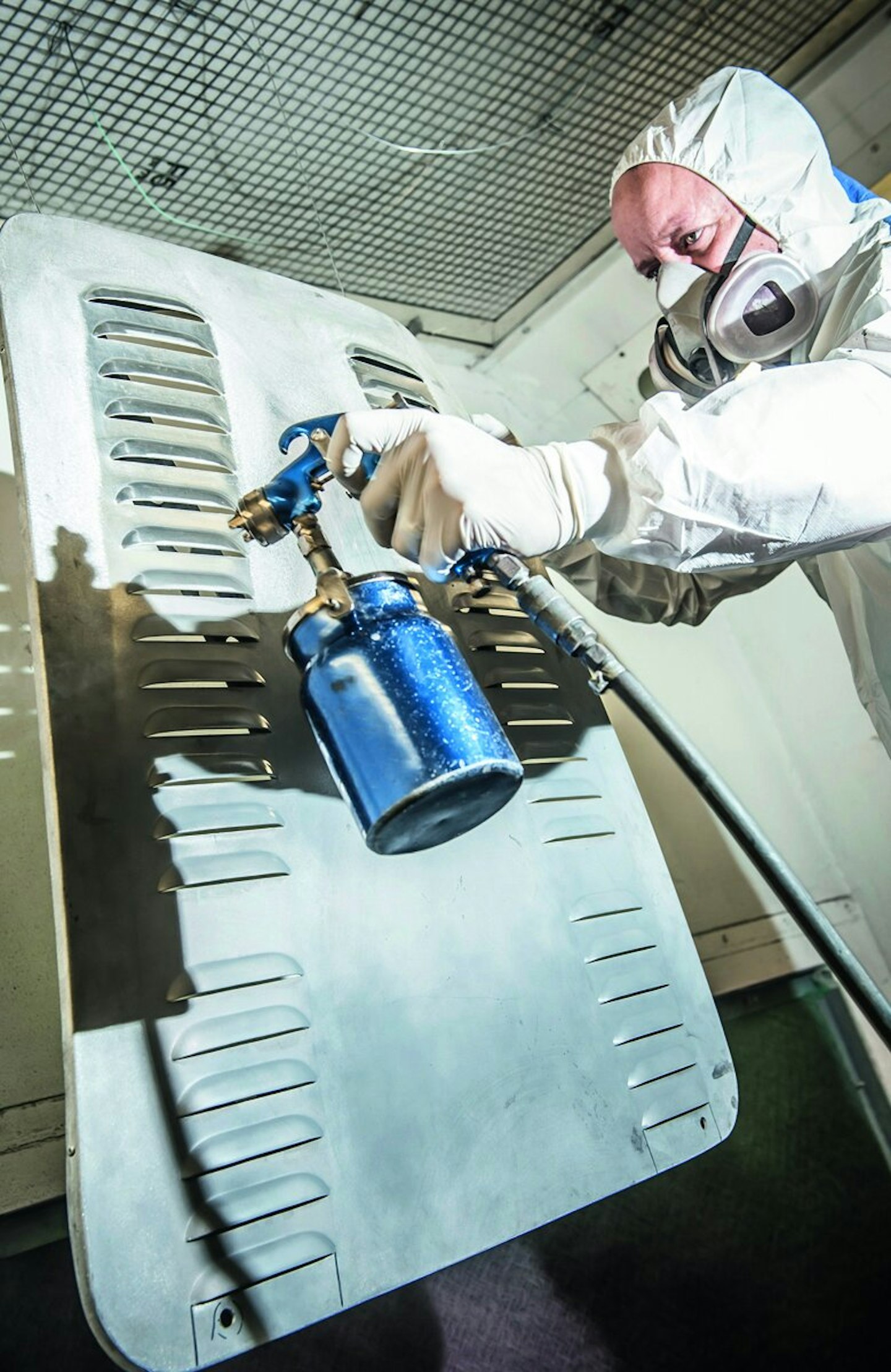
The insides of the doors, bonnet and bootlid have also been painted by now, so all the panels are wiped, gone over with a tack-rag and degreased before masking up to apply the Old English White on the flanks. The car was all-red, but the creamy-white flanks were popular in 1962 and look fabulous. Opening panels are painted off the car, but the doors have to be fitted to get the masking lines right. Then they’re taken off again.
After Paul has applied, flatted, re-applied and re-smoothed the OEW, it’s time for three coats of high-solids lacquer. No ’Healey had this in period, but it gives an extra-deep, lustrous finish. Paul wet-flats the lacquer with P3000 then spends two days machine-polishing with Farécla G3 compound.
‘It would have been done in cellulose originally,’ he says, ‘but it fades and goes chalky, takes six weeks to harden and is brittle. Two-pack is easier to work with.’
“The steering wheel is new because the old ones crack”
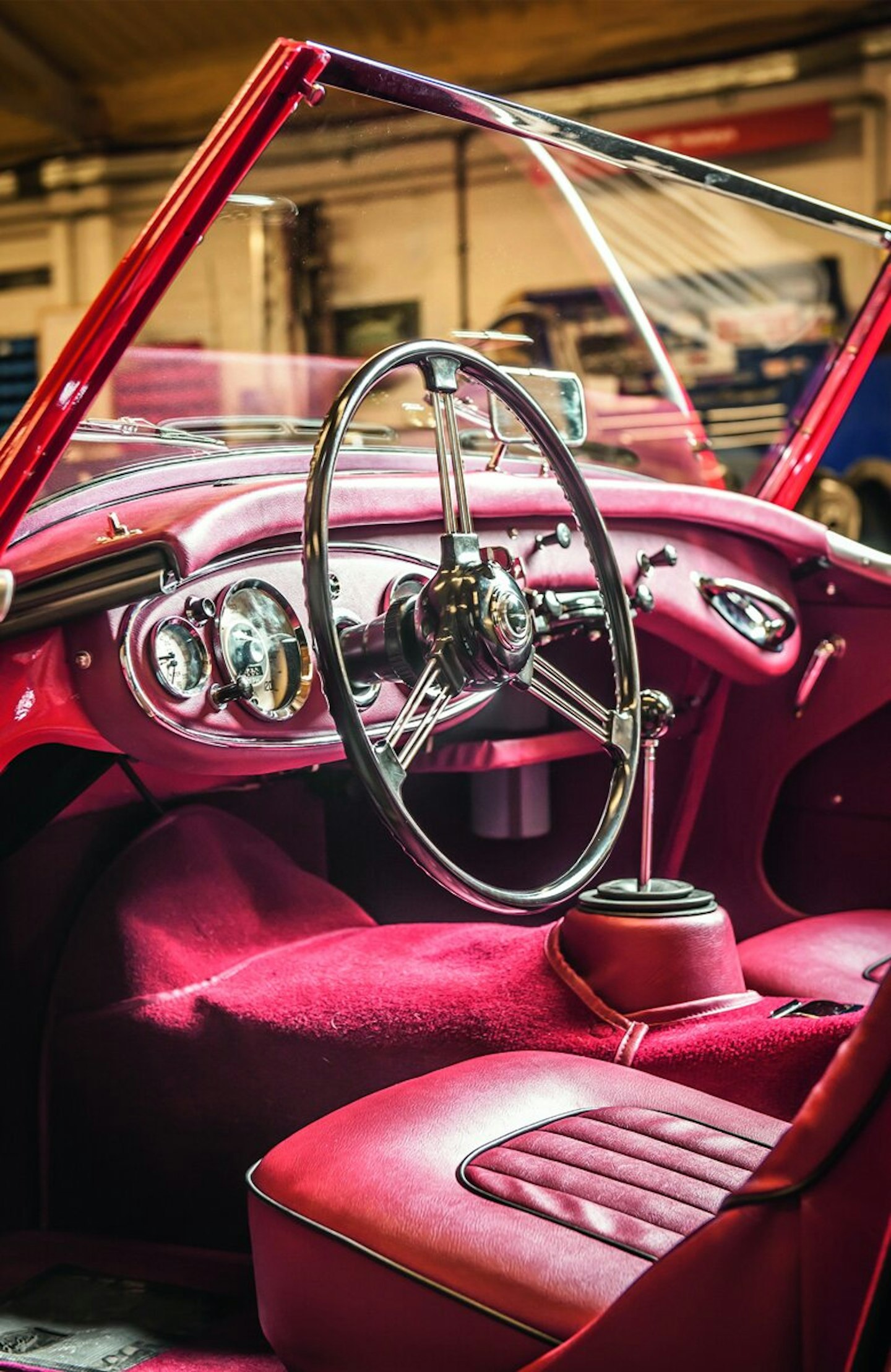
INTERIOR
‘There were animals in the seat foam,’ Chris reports, ‘probably mice. All the panels with a card or thin plywood backing were in a sorry state. And there was that right-hand drive dashboard.’
But it wasn’t all for the skip. The front seat frames and rear seat pans could be re-used, and ‘our lady trimmer’ re-trimmed the front seats. JME makes new door trims, while the rear seat and side panels are outsourced. The instruments are reconditioned by a specialist, the steering wheel is new because the old ones crack, and new carpet is cut and laid.
There’s a tailor-made hood and tonneau but the frame is original, as are the windscreen pillars and their chrome trims. The aluminium moulding which defines the cockpit edge is, importantly, also original albeit beautifully re-anodised.
“The engine was suitable for a problem-free rebuild”
RUNNING GEAR
As found, VSU 901 was complete and the crankshaft turned freely – so it must have been very tempting to see if it would fire up and run. ‘Yes, we were tempted,’ admits Chris, ‘but with those triple carburettors and lots of scope for trouble… So we said, “let’s just strip it.”’
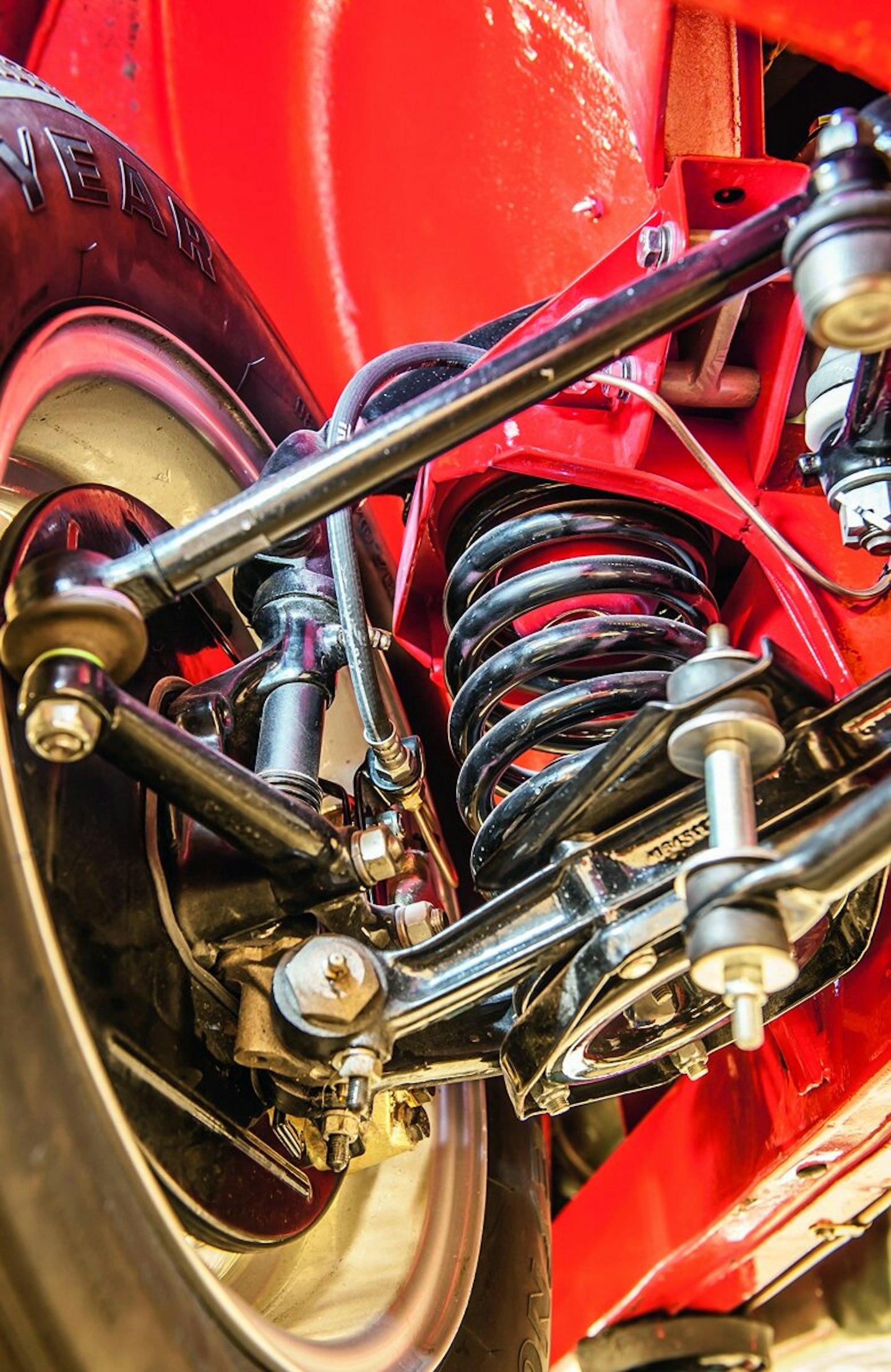
With the engine apart, it was good news. The crankshaft was in extremely good condition, and the whole engine was suitable for a problem-free rebuild. JME’s engine whizz, Carl Mason (pictured above), had the cylinder block bored to +.030in (it was already at +.020in), the ’head skimmed and fitted with new valve guides and hardened seats, then fitted new pistons, camshaft, tappets and bearings, and new anything else not fit for re-use. The gearbox needed new baulk rings and one synchromesh hub but was otherwise fine, helped by the oil that had stayed in all those years. The overdrive needed a light refettling, which JME did on site. The back axle was pleasingly low on wear and just needed new bearings and re-shimming. As for the steering box, a left-hand drive unit and complementary idler box were found to allow VSU 901 to return to its original configuration. ‘It was in pretty good nick,’ Chris says. ‘We just changed the peg – the worm was fine – and the bushes and seals.
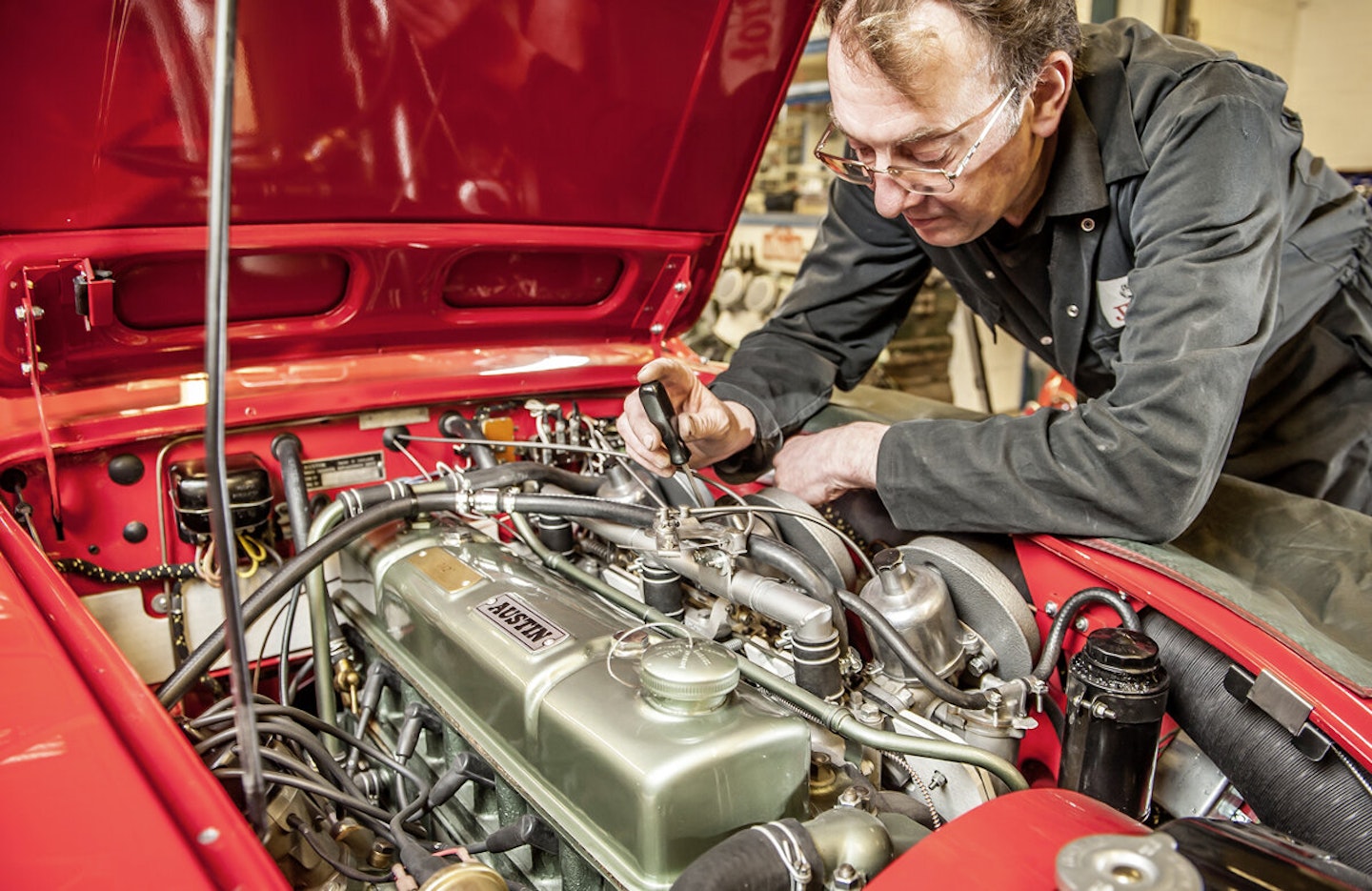
‘When the car was stripped we had a huge pile of suspension bits for powder coating: springs, uprights, arms, brackets and more. We used all the original springs; the rears can sag, but these hadn’t. AH Spares reconditioned the lever-arm dampers and we reassembled it all with rebuilt kingpins, new wheel bearings, new rubbers and new brake hydraulics.’
The 72-spoke wire wheels are the originals.
EXPERT TIP
Building a reliable, durable engine is vital for JME, and a unit’s age is no excuse for bad mechanical behaviour. The cylinder block and ’head are acid-dipped, crack- and pressure-tested, and treated to ‘space sealing’ – a two-coat ceramic sealing process that fills any light cracks or porosity in the waterways. ‘We do that because these engines are getting no younger and the castings aren’t great,’ says Chris. Thus oil and water are kept strictly separate.
FINISHING
“It has its original handbook but we need a 1962 toolkit”

All the electrics are the domain of Mick Wood (left), who refitted components rebuilt by ex-Lucas expert Terry Dodds, who also made the wiring loom. As with the cockpit moulding, so with the front grille whose surround was originally fitted and tweaked for each individual car. JME rechromes this as one unit rather than dismantling it.
The bumpers, however, are new stainless items which have been chromed. Asbestos was common in 1962, but this time around the heat shields in the engine bay have been remade in modern builders’ insulation board.
Only in its electronic ignition, negative-earth polarity, larger radiator core, 70-profile tyres and hidden 12V sockets does VSU 901 depart from mechanical originality. It even has an original 1962 handbook. ‘But we still need to find a 1962 toolkit,’ adds Chris.
“This ’Healey now feels like a new car – which it virtually is”
THE RESULTS
‘It took us 18 months because it was our own car,’ Chris reflects, but when there’s such a high flow of cars – 114 came through the doors last year – it’s hard to devote time to your own project. We did nearly everything in-house, so we could keep control and maintain quality. It probably took about 900 hours.
‘If we’d charged a customer for it that would have been £25,000 in labour and £26,500 in parts. Plus you need the car in the first place, say £18,000 for one in the state this was in.’ On that basis the £75,000 asking price seems very fair. JME is a business and the ’Healey must be sold, but the Everard brothers definitely have a sentimental attachment to it.
I can report that this 3000 is now a delight to drive, taut, torquey, tuneful, just a little bit vintage and feeling like a brand new car – which it virtually is. A brand-new car, built in an original ’Healey factory building. Perfect.
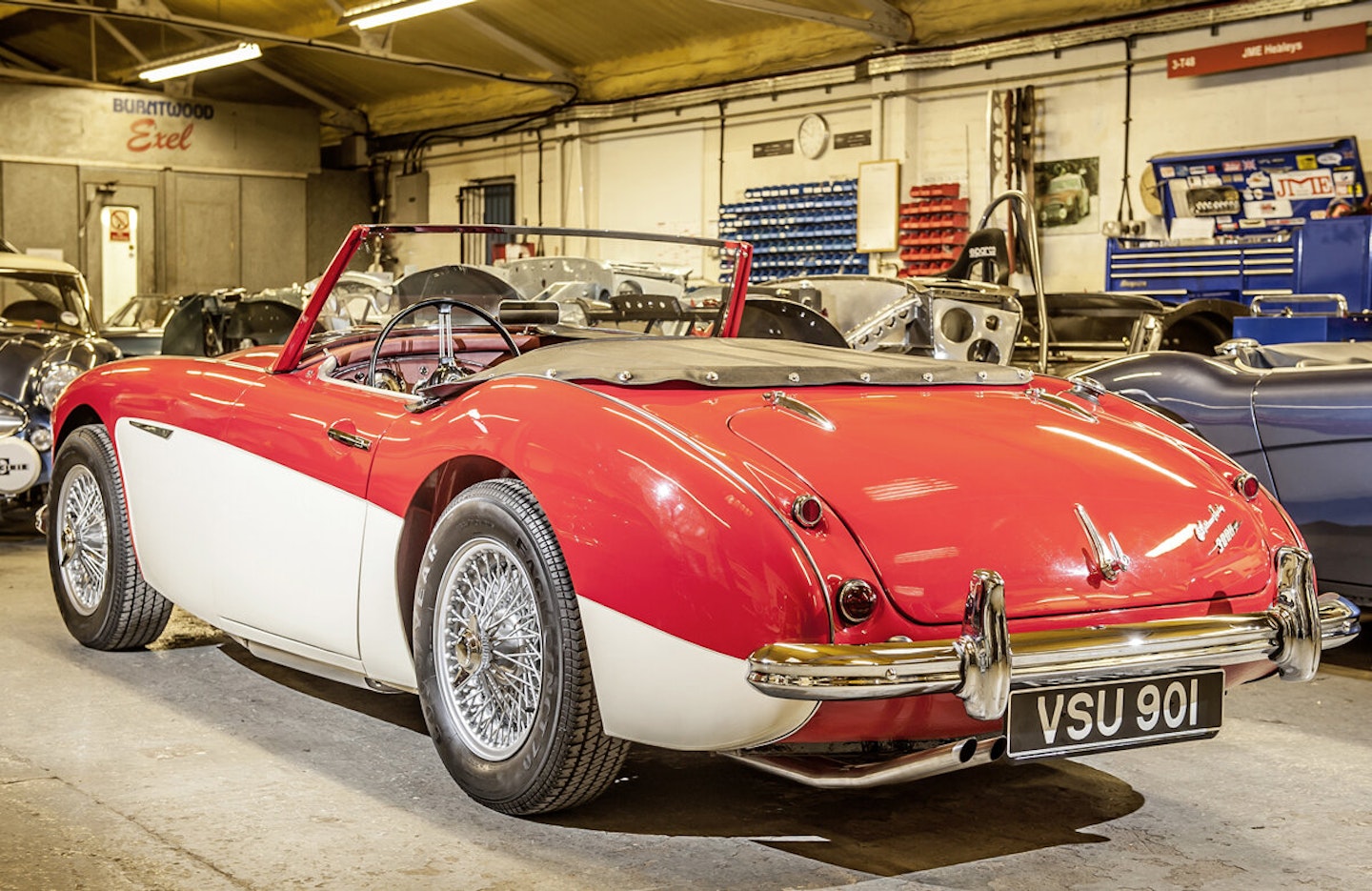