It took one Bentley specialist six years just to buy this car – then he was asked to do a total restoration in only nine months
Words NIGEL BOOTHMAN Photography LAURENS PARSONS
The market for Bentley Continental Drophead Coupés, especially the S1, has been heating up for some time. Giles Crickmay of famous Rolls-Royce and Bentley specialists Frank Dale and Stepsons candidly admits to having a waiting list for the cars. ‘I’m always keen to find them because there are half a dozen people waiting for a phone call. The trouble is, they don’t change hands often, and sometimes you need to apply a great deal of patience.’
The perfect example of this is the car seen on these pages. Crickmay first heard about it nearly eight years ago at the annual Techno Classica show in Essen, Germany, as he recalls. ‘A German doctor introduced himself and said that he had an S1 Drophead; he showed me some pictures of it. It looked a bit sad, but
I asked him if he wanted to sell it. He said no, he was going to keep it and start using it again. This happened again the next year, and the next – in the end I stopped asking him. Then, in 2012, he came to our stand once again and, after we’d chatted for a while, he said, “Aren’t you going to ask me?” So I did – he said yes, he would sell.’ Crickmay already had a customer for it.
Back in the UK, much work to brakes and suspension rendered it driveable, if tired and tatty. In October 2012 the new owner, Jeremy Barrett, returned it to Frank Dale and Stepsons’ workshops on the edge of London so the restoration could begin.
His enthusiasm for the car created a nerve-racking deadline. ‘He said he wanted it completed in time for a summer tour down to a concours event in Italy. That gave us barely nine months,’ says Crickmay. ‘I thought it might be possible – if we were lucky.’
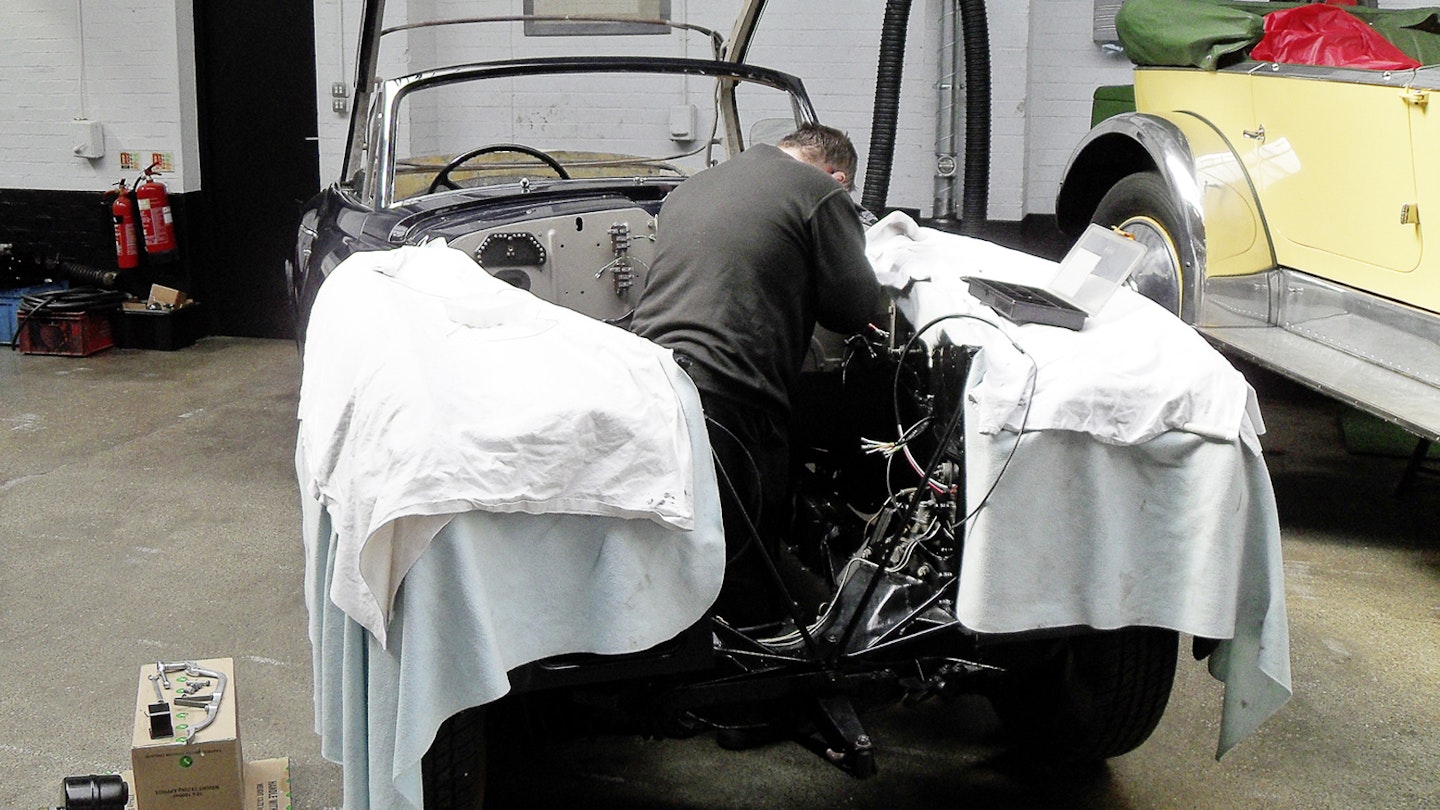
‘We’re going to keep it for a long time, so it had to be done exactly right’ – Jeremy Barrett, owner
Jeremy Barrett has fed an enthusiasm for exciting cars with more modern machinery from Ferrari and Maserati, but he fixed his sights on an S1 Continental Drophead some time ago.
‘I had guidance from Bentley-owning friends, which meant my first foray into the classic car world was a fairly well-informed one. I knew exactly what I wanted, which was a problem because there were only 55 right-hand-drive examples made. I had to wait two-and-a-half years before I got the call from Giles Crickmay.’
Barrett was also very clear about the need for a project car rather than a concours example. ‘I knew I wanted the car to be specified to my requirements, so it seemed crazy to pay twice by choosing a restored example and then having it all done again.’
The flipside of this route is of course the unknown state of the car beneath the surface. ‘In the end, it took longer than we hoped but you have to accept this. I wanted some features that hadn’t been done before, like the concealed zip for the rear window, which was an idea I got from a Porsche 911 cabrio I once had. I’m not someone to leave cars in the garage, and it will get used. The whole family can ride in it and we all like it – even my 15-year-old daughter who isn’t the least interested in cars. We’re going to keep it for a long time, so it had to be done exactly right.’
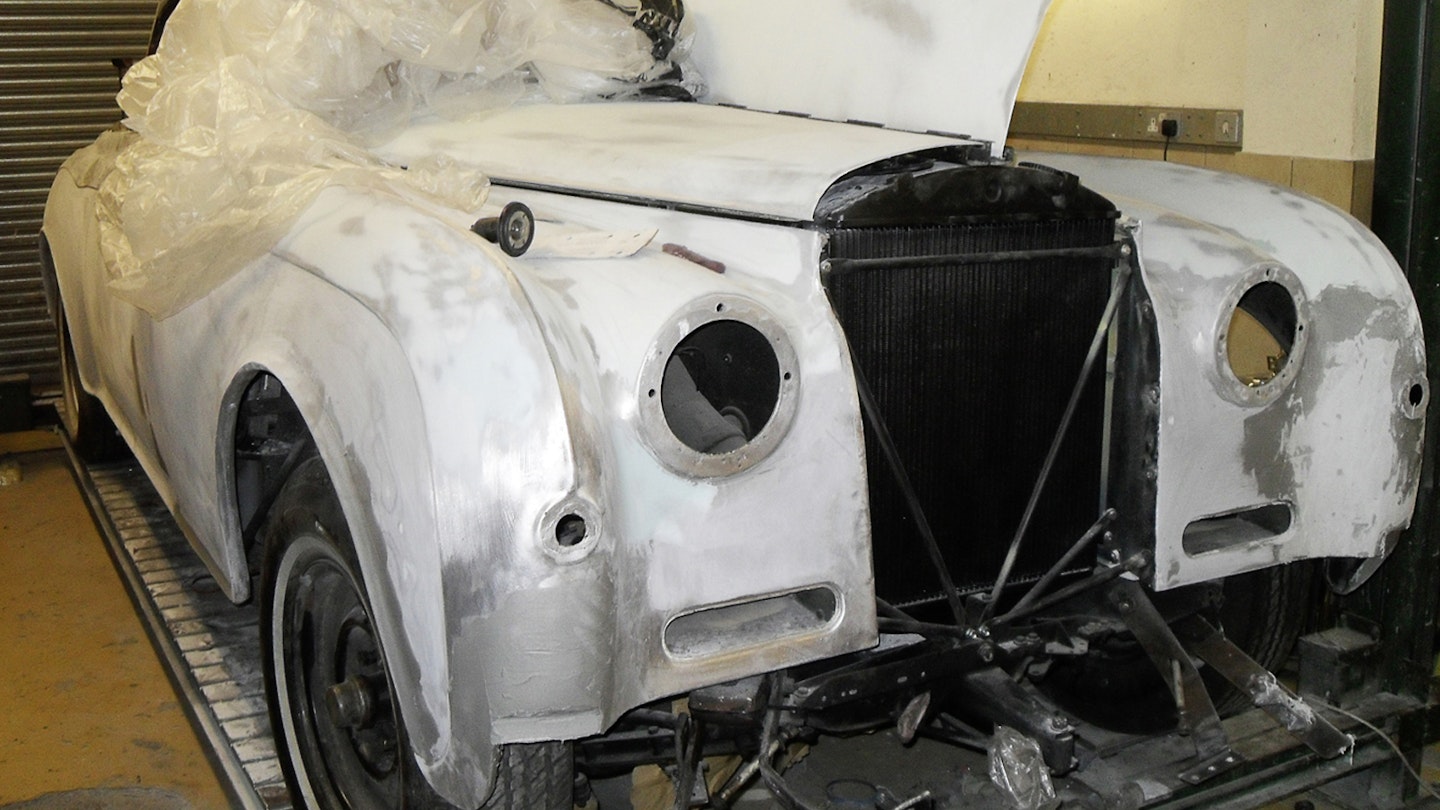
‘Pretty soon we realised we weren’t going to be lucky’ – Giles Crickmay of Frank Dale & Stepsons
Body, chassis and paint
‘It had been restored in the Eighties,’ says Crickmay, ‘but it really wasn’t done well. The paint was bubbling in lots of places and we weren’t sure exactly what we’d find once we’d got the project under way.’
The work was carried out by Frank Dale and Stepson’s coachbuilders, who took care of the whole process from metal repair to paint and re-fitting. Crickmay’s task was to oversee all the work and make decisions that could have a profound effect on the time taken. As, of course, could the condition of the coachwork itself.
‘Pretty soon we realised we weren’t going to be lucky – it was a lot more corroded than we thought,’ says Crickmay. ‘Every exterior panel needed something done, from corrosion or damage repair to re-gapping. It also needed significant repair to structural steel areas under each door, though the chassis itself was perfectly okay, requiring only cosmetic attention. This allowed us to leave the body on the chassis, so the body would remain well supported through the process of repairing the sills, and it would save considerable time in a restoration where the clock was running.’
Any splitting of body and chassis inevitably takes up twice the space and creates time-consuming hassles when the body is to be moved, for instance from a repair jig into the paintshop – it’s no longer a rolling unit. And with such weak sills, the most involved repairs would probably have to be done with the body still on the chassis anyway, to keep it stable.
‘We cut away both of the box sills,’ says Crickmay, ‘with new ones fabricated from scratch. They’re large, important structures and contribute a lot of strength.’
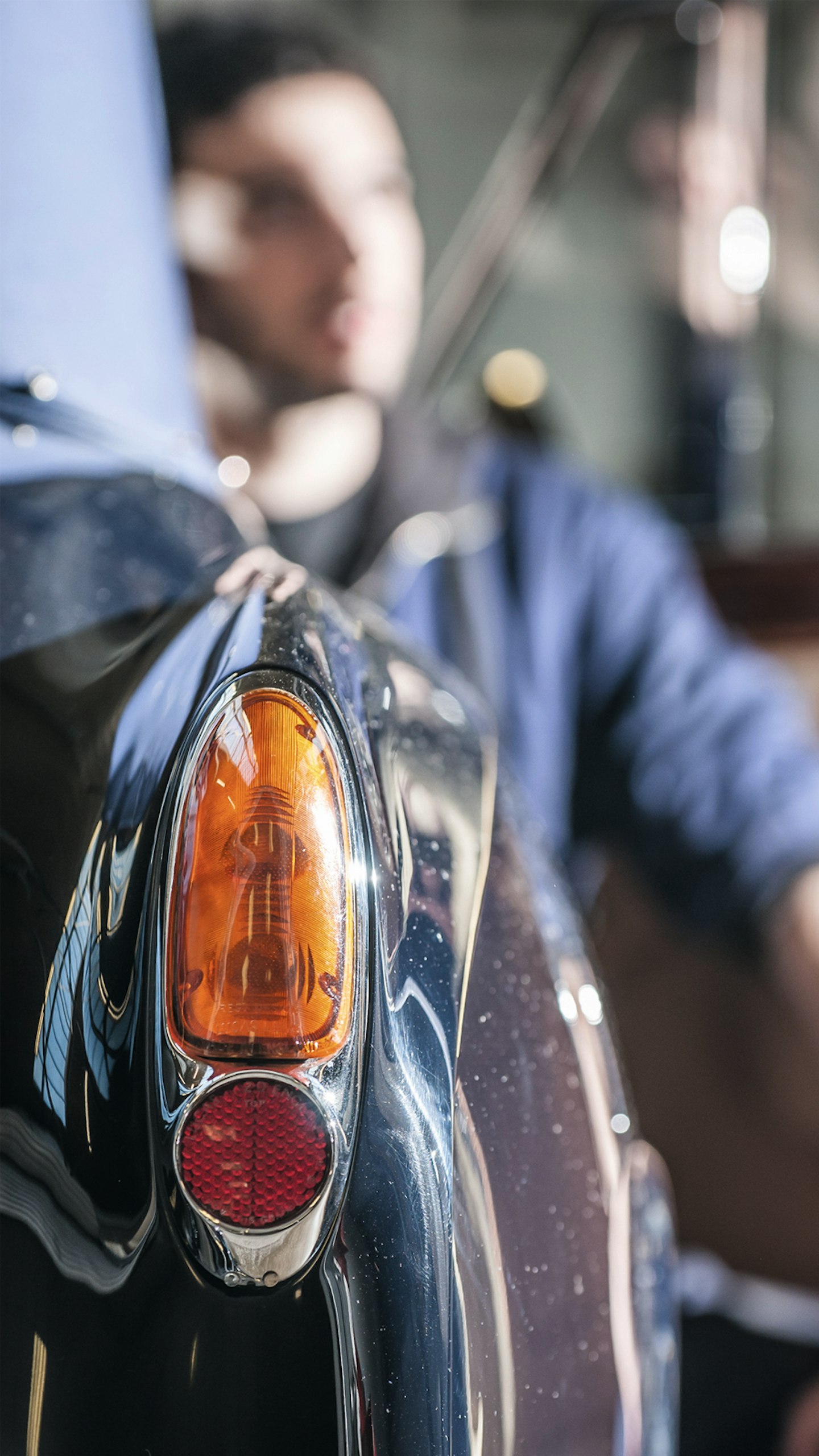
The rest of the metalwork was mainly to the aluminium panels – all the visible parts of the Continental’s Park-Ward body are aluminium.
When the welding and panelbeating were completed, the team used a special aluminium filler to cover the minor imperfections but also to show up uneven surfaces, as Crickmay explains. ‘It goes on like cake icing, then dries to a grey-white finish.
‘It’s blocked down to reveal any low or high spots, which can then be corrected.’
One dedicated adherence to originality was the labour-intensive choice of cellulose paint, now unavailable except for use on classic cars.
‘We had to provide the car’s registration document to prove its age before we could buy the paint,’ says Crickmay. The colour is Oxford Blue, a Rolls-Royce/Bentley shade from the period.
Accurate attention to paint details did not end with the exterior panels. ‘The bulkhead and underside of the bonnet was painted in the correct shade of Sand, while the engine bay sides were sprayed black, as they should be,’ says Crickmay.
‘Even the cosmetic work involved in getting the chassis to concours standard took 200 hours – the work by the coachbuilders was the most time-consuming aspect of the whole job.’
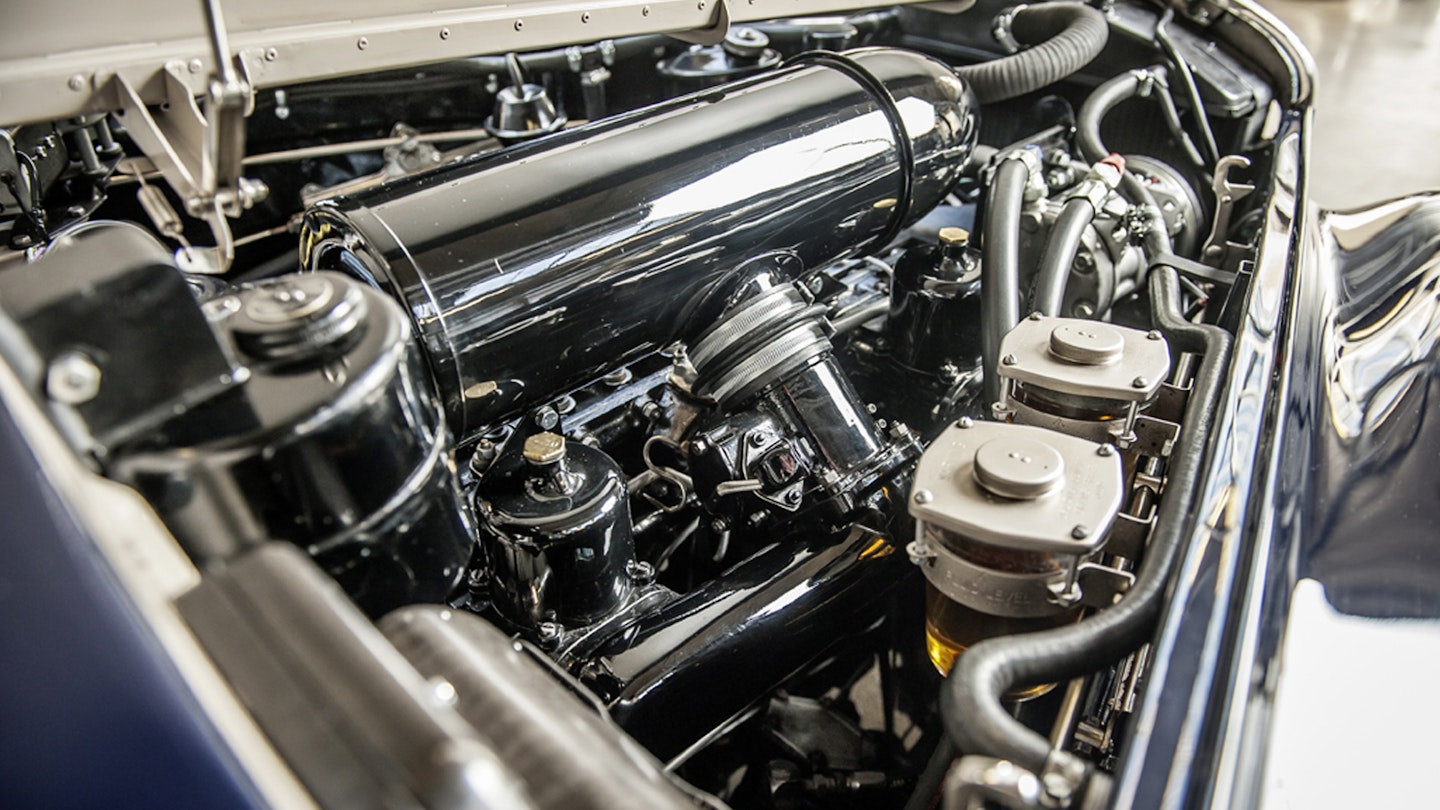
‘It seemed tired and the only way to be sure was to strip it’ – Vincent Roma, workshop manager
Engine and running gear
As received, the Bentley was running, and following extensive work to the brakes and suspension, roadworthy. To hit the original target of early summer, 2013, the engine would need to be good enough to get by with a paint job and renewed or refurbished ancillaries. It was down to Vincent Roma, the man in charge at Frank Dale and Stepsons’ workshops, to decide.
‘I had my doubts,’ he says. ‘It seemed tired and, in the end, the only way to be sure was to strip it. We removed the cylinder head first to make the engine lighter and easier to remove as one unit with the gearbox. Sure enough, new pistons and cylinder liners were going to be needed, along with a crankshaft re-grind.’
This helped to kill off any remaining hope that the original deadline could be met. At least one piston had suffered with broken rings, which in turn damaged the liner. The advantage of removable cylinder liners is that the engine block could be re-used, as could the cylinder head. This was fortunate, as they are unavailable without using parts from another engine. This car, being a late S1, had the larger twin carburettors, twin brake reservoirs and power steering from new, but we’re often asked to upgrade earlier cars to this specification. We do this using original Bentley parts, but on this car the only major change was the addition of air-conditioning.’
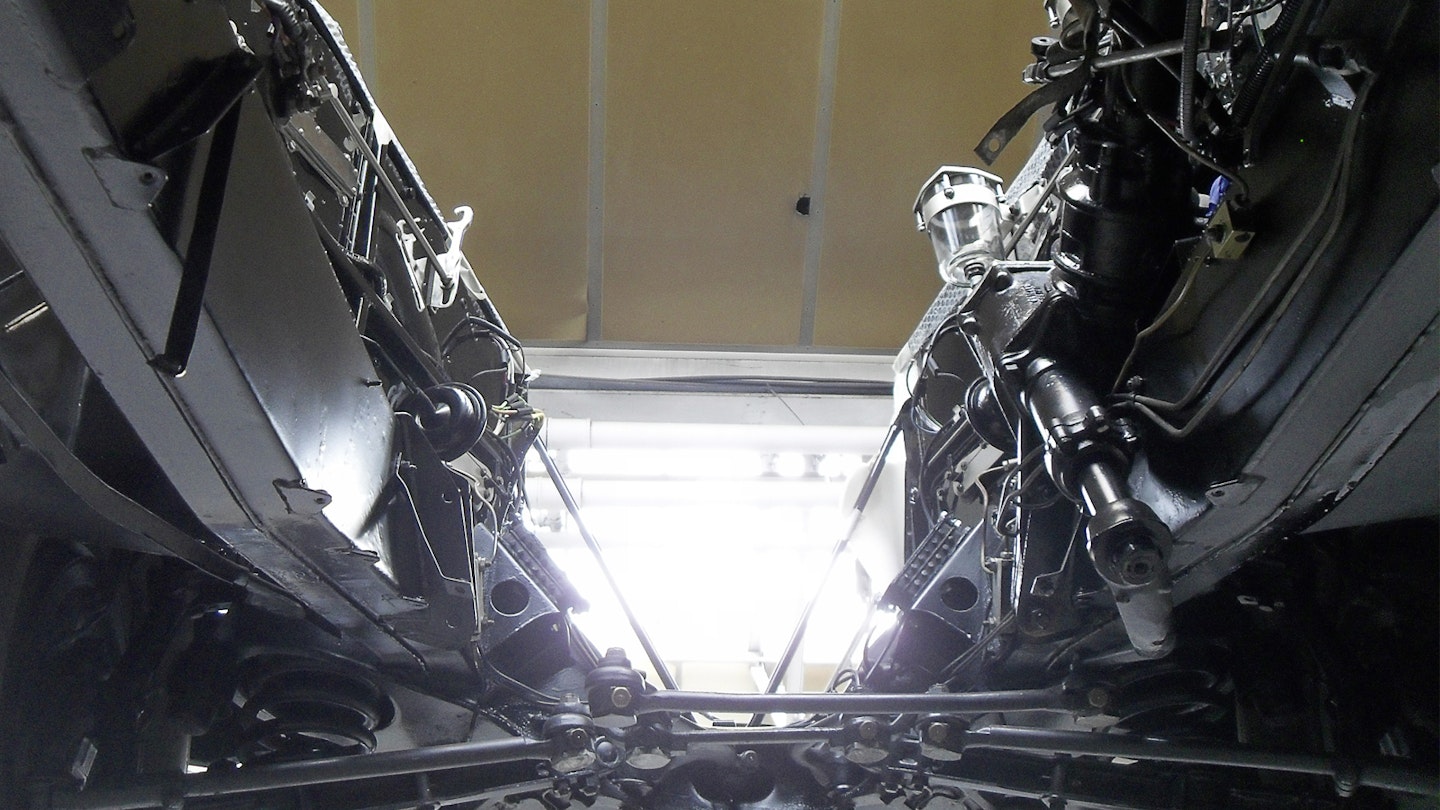
The S1 Continental used a four-speed Hydramatic transmission, a General Motors design licensed by Rolls-Royce. This needed attention, but the American origins of the box make for superb parts supply, says Roma. ‘We do so many of these gearboxes that the rebuild was straightforward, even if it used up more time. It needed new clutches and bands – they often do.’
Some of the smallest jobs in the engine bay became the most time-consuming, as the owner’s aims for concours success shifted up a gear.
‘When the car was pretty much finished, the customer asked us what could be done to take it that final step,’ says Roma. ‘I pointed out various items that judges might pick up on. Bentley S1s have two taps on the nearside of the engine that you can turn off in summer when the heater isn’t in use, and while the ones on this car are original, they need to be cadmium-plated.’
Hours taken: 300
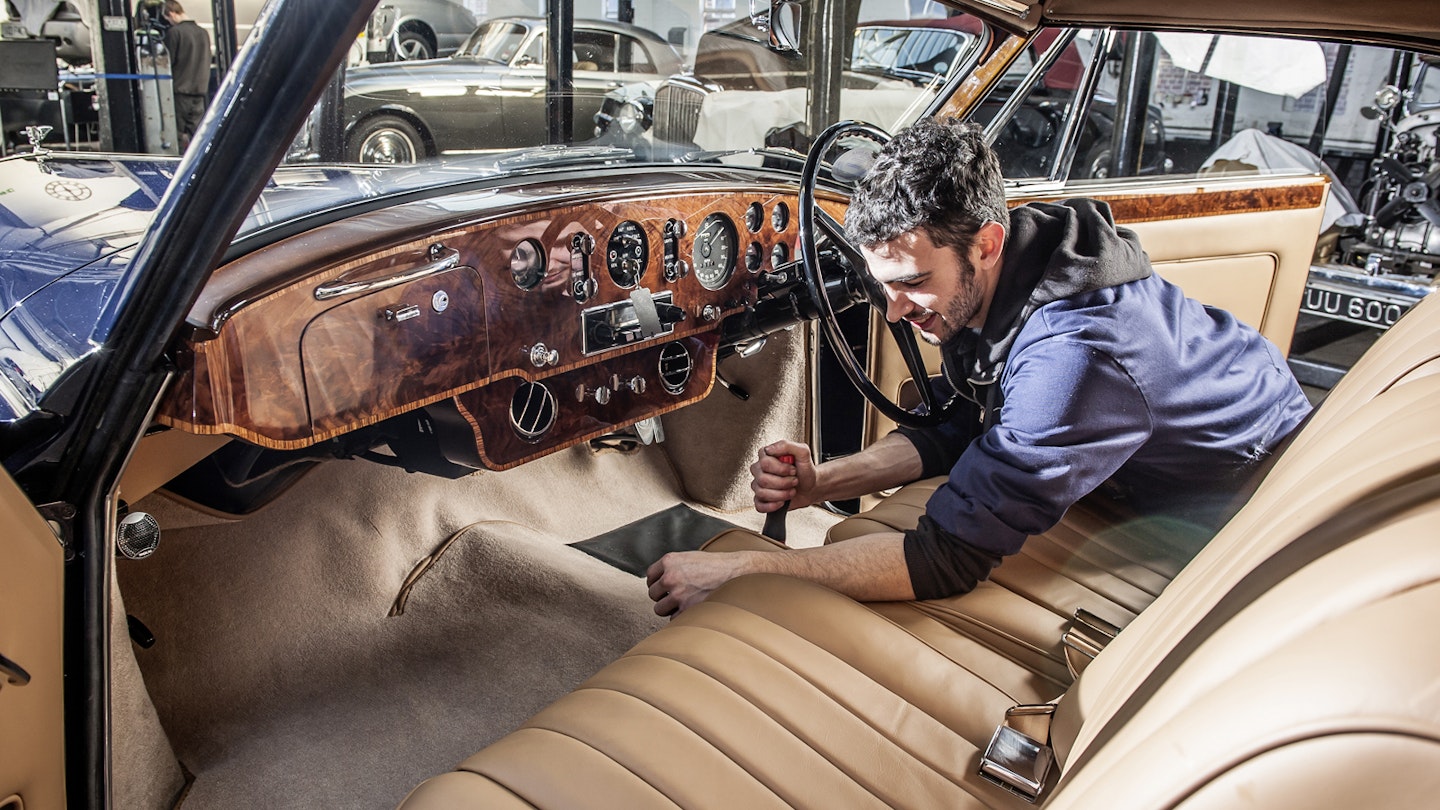
‘Everything is a bespoke job, as each car was different’ – Luke Turton, interior trim
The trim
Luke Turton looked after the trim, from carpets up to the roof. The existing leather was intact but grubby and not well-executed, making for an ill-fitting look. Likewise, the hood bag was a poor fit and the hood fabric itself was baggy on its frame.
‘Everything is done as a bespoke job, as each car was handbuilt and they all differ. With this car, the materials that came out gave us something to work to, but a lot of it could have been better, so we made numerous adjustments,’ he says.
The wood veneer was particularly bad. Turton and his colleagues prepared these pieces and sent them out for re-veneering; everything else was done in-house.
‘It’s not just the leather itself that needs attention,’ says Turton, ‘the seat frames, runners and padding can all suffer. We found that only about 65 per cent of what we removed could be re-used, but that’s actually pretty good – we see a lot worse.’
It’s not only the seats that are padded. Between the English mohair that makes up the outer surface of the hood and the woolcloth lining, Turton had to pack the space very carefully. ‘We use something called white wadding, which is a synthetic packing material that shouldn’t ever rot and which should hold its shape much better,’ he says. ‘You need it to create the right profile that gives the roof a correct shape when it’s up.’
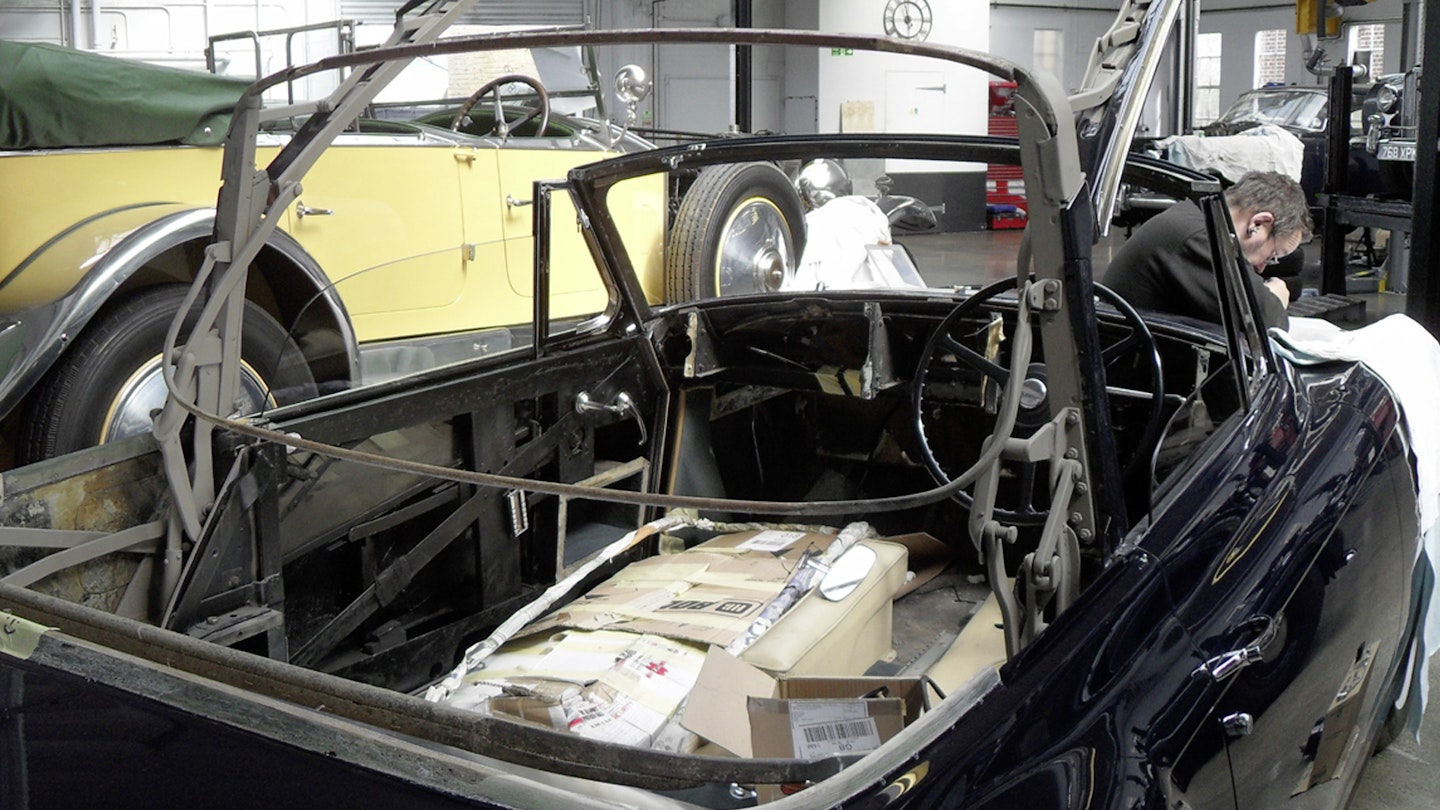
The roof is powered, erecting and descending smoothly at the touch of a switch. It’s driven by a motor and a ram below the rear seat and this, together with the roof frame, was the one aspect of the car that worked perfectly and did not require rebuilding.
However, any time saved was then consumed by finding a way to satisfy the owner’s request for a zip-out rear window. ‘He asked for it to be done in such a way that you can’t tell it’s removable and we worked out a way to hide the zip. The window itself is 40,000 Vyback – the number refers to the thickness, and Vyback is the durable clear plastic it’s made from.’
Hours taken: 300
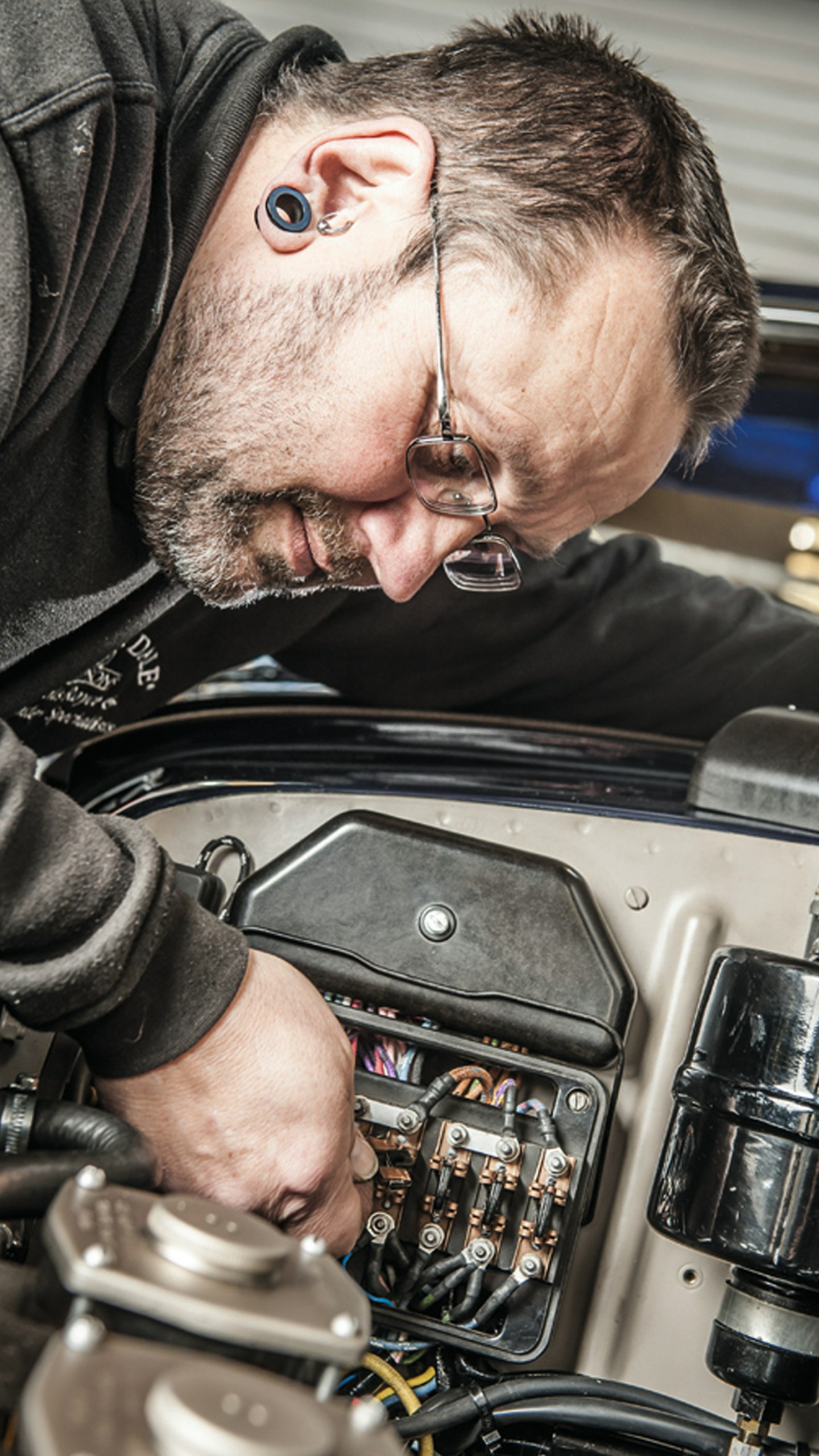
‘During the initial stripdown, every single wire is removed’ – Kevin Denison, electrics
Electrics and mods
This car features a number of 21st-century upgrades, though the owner’s brief was for it to look just as it did in 1959. Before any changes could be implemented, the very Fifties wiring had to be entirely renewed by Kevin Denison, pictured above. ‘During the initial stripdown of the car, every single wire is removed – earth straps, the lot. We even take the clips off the chassis that hold the loom, blast them and re-paint them.
‘We like to re-use as much as possible – those chassis clips are held in with tiny 2BA studs and I went to a lot of bother to get them out rather than break them because the new ones are a different shape.’
The new loom is made from the correct fabric-covered wiring and can be bought off the shelf, though Denison’s life isn’t simplified that much. ‘The spade connectors they use, about 60 of them, are metric and I need to trim every single one by about 1⁄16th of an inch.’
Wiring to suit the original 25-amp dynamo needed upgrading – even new 25-amp wiring is no good for the 70-amp alternator the car now runs. There were sufficient modifications made to this car for Denison to create a separate power stud for the ancillaries, such as the stereo, amplifier and air-conditioning.
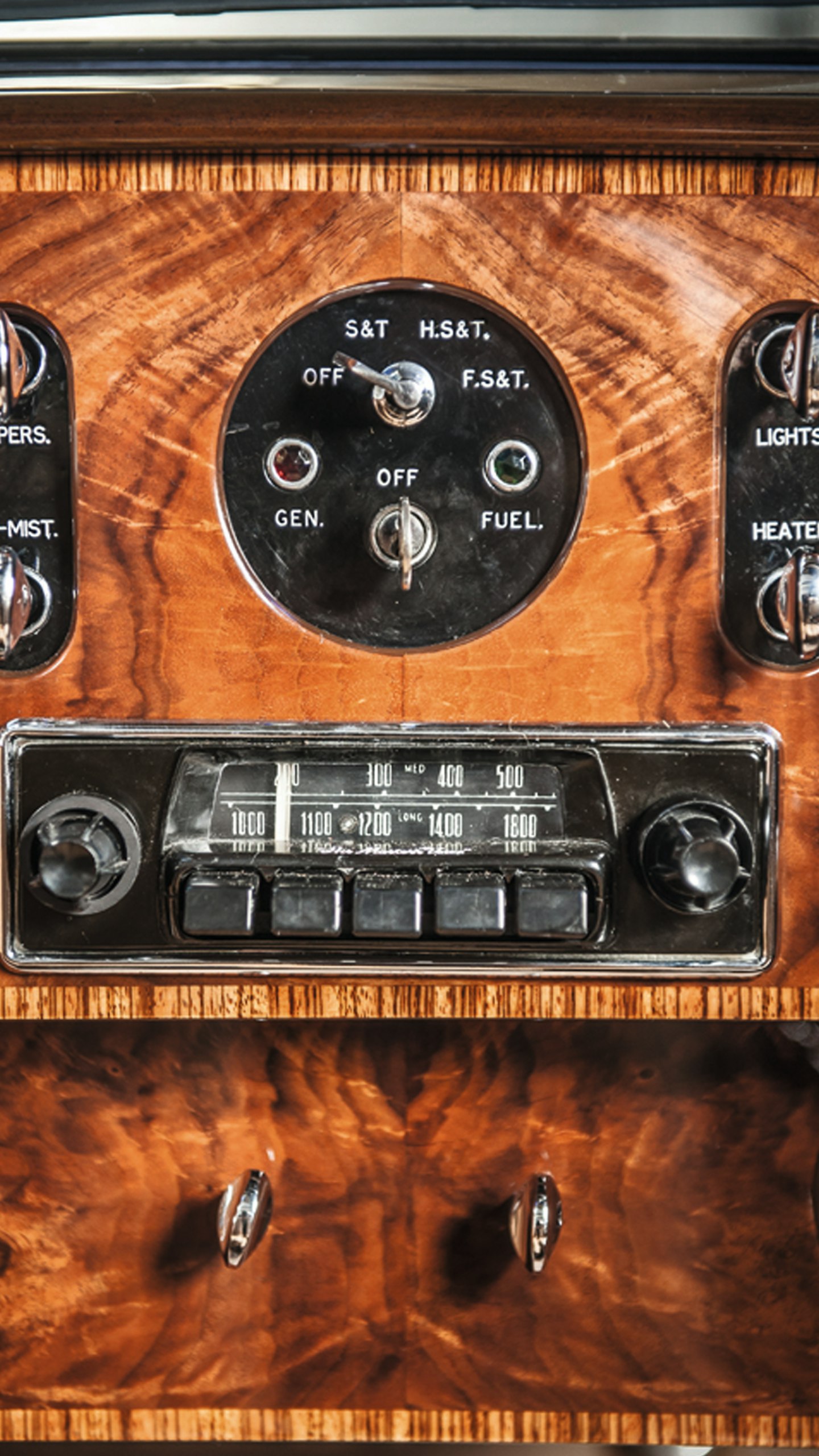
‘The stereo is in the glovebox with an infra-red extender allowing you to control it with a remote without opening the glovebox door,’ says Denison. ‘There’s an amplifier concealed by a panel in the boot powering speakers in the parcel shelf, under the rear seats and up under the dashboard: 150 watts per channel, times six!’
Even more up-to-date is a tiny Bluetooth microphone to allow the stereo to work with a mobile phone. For the air-conditioning, Denison worked alongside the trimmers to send cold air into the custom-made, wood veneer-faced aircon panel under the dash. The ‘eyeballs’ that direct the air were sourced from a Rolls-Royce Silver Shadow and the knobs are bought-in items, machined down and threaded to suit.
There are lots of other neat touches – a brighter boot light, a blacked-out and therefore invisible air-conditioning condenser behind the grille – but the cleverest stroke is the dashboard lighting. Bentley S1 dash illumination is so poor as to be almost useless, but Denison came up with a way of inserting white LEDs in the very edge of the dials.
‘I used three LEDs in each small dial and 12 in the large ones. They’re hidden by the dark surrounds on the glass and now every dial is legible all the time.’
Yes, the restoration over-ran to just two days less than a year, but that’s entirely typical of the unforeseen challenges most projects conceal and it’s still pretty fast for such a large job. With a return to the workshops for post-restoration fettling now complete, 2014 promises to be a very enjoyable year indeed for the owner of this remarkable, immaculate Bentley.
Hours taken: 300
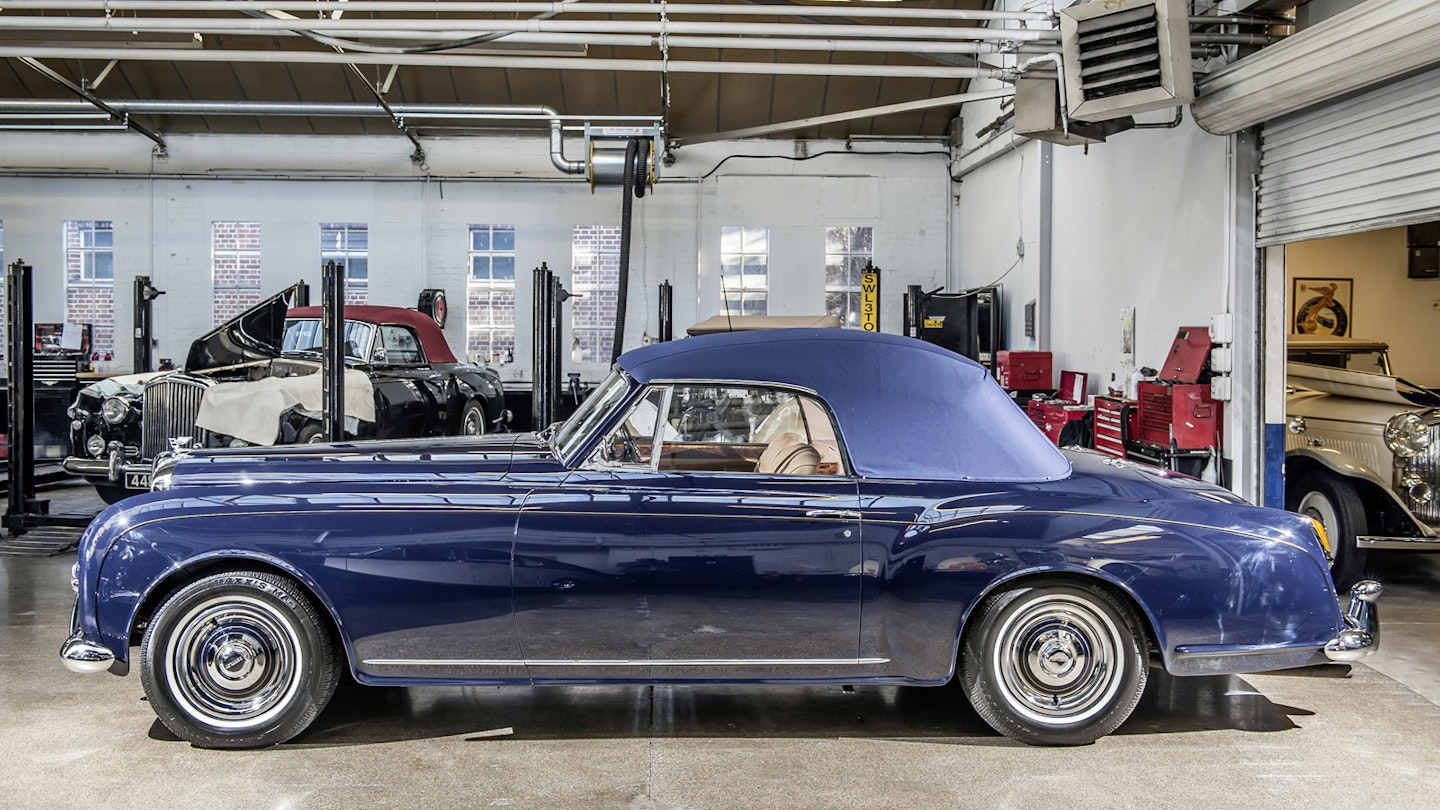