This Jaguar E-type had suffered a rollover, being shot at and left in the elements for 40 years. A brave restoration then Something happened to this car in the mountains of New Mexico in 1971. Something bad. It probably involved evasive action, a terrifying skid and then a sickening rollover. The roof collapsed on the right-hand side, pillars folding like broken twigs, the tarmac battering the wing tops as the car slowly came to a halt.
Once it was righted, the extent of the damage clearly put off any ideas of fixing it. By this point, this Old English White Jaguar E-type FHC was nearly ten years old having been imported new in December 1962. Whoever took ownership never got round to scrapping it, but instead the years took their toll via 40 years of outdoor storage.
‘The paint had been blasted off by the desert sand,’ says Richard Feather. He’s the man who bought this car as the result of a bold moment online on New Year’s Eve 2012. ‘There were some bullet holes too, and they looked like a pretty large calibre. We still wonder what happened.’ He later found an online article written about this E-type at the time it was advertised, describing it as ‘one of the most thoroughly thrashed examples we’ve ever laid eyes on’.
Richard had never owned a classic car before, never mind restored one. Nonetheless, he had a clear vision to rebuild his E-type for the best driving experience. ‘That meant being faithful to its original design and engineering,’ he says, ‘but it also meant adapting it for 21st-century driving and correcting its known foibles with, for instance, better cooling and brakes.’
Without a recommendation for a decent Jaguar specialist, he was reduced to checking out different options thrown up via a web search. His search ended with Adam Booth of ATB Classic Car Restorations.
The state of the car as it was bought says a lot about Richard Feather’s personality – he comes across as buoyant, cheerful and optimistic. As you would need to be if you clicked ‘buy it now’ on a car like this. Not every restorer would agree to take on such a job, but in Adam Booth, Richard had stumbled upon a kindred spirit. Adam works alone in his workshop in South-West Wales, sub-contracting certain jobs but doing the bulk of them himself. ‘So we embarked on this huge restoration,’ says Adam. ‘I began stripping and repairing the car with Richard sourcing the parts as and when I requested them.’
All of which requires resourcefulness, confidence and a can-do attitude. Whatever arrived on that trailer, whatever state it was in, was going to be fixed. In the event, it needed work just to get it into the workshop.
‘I had to change the wheels while it was still on the trailer just to get it to move,’ says Adam. ‘After that, I could start having a proper look at it. It was full of holes, apart from the bits that were full of spiky tumbleweeds and dead mice. The cylinder head was off it, the inlet manifold and carburettors were wedged in the boot and the interior trim had mostly been eaten. But the biggest problem was obviously the roof.’
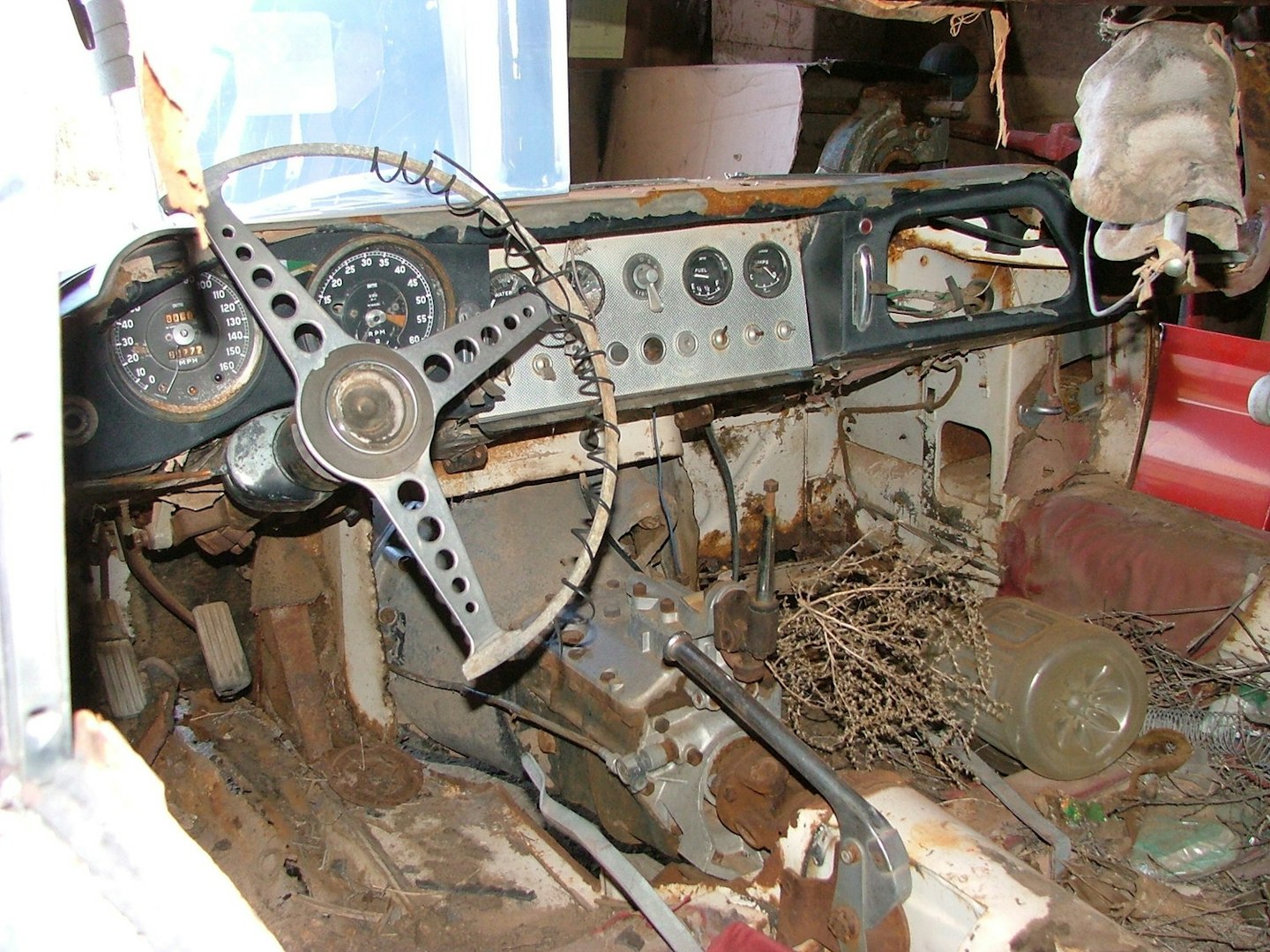
Lifting the lid
Before any further structural work could begin, Adam needed to establish just how bad the damage was.
‘I obtained a body jig some years earlier for an S1 E-type,’ he says. ‘Once I’d stripped everything off the car – all the running gear, driveline and so on – I could mount the tub on the jig and to my relief it showed the car wasn’t twisted.’
Adam’s plan for the roof was to jack it up and push it back to a repairable state, but found it wasn’t possible to undo that amount of destruction. ‘The roof and tailgate were beyond repair,’ says Adam. ‘Richard found a guy in America who had a roof panel and a tailgate spare. So I exposed the factory joins in the C-pillars, sweated out the lead and then drilled through the spot welds. That got the old roof off.’ Adam was able to measure another E-type to construct an internal jig that gave him a good idea of where the new roof should sit on Richard’s beheaded car.
‘There are internal panels in the C-pillar as well as what you see from the outside,’ Adam says. ‘I straightened the original ones both inside and out and then slowly positioned the new roof, screwing it in place to check every gap before I started welding.’ Because new glass was required all round, the new screen would define the front edge of the roof, leaving Adam to get all the spacing correct further back. ‘The new roof was very slightly bigger than the original, but I got it exactly where it needed to be. Then I could replicate the factory spot welds.’
Adam’s resourceful approach came to the fore again when supporting the roof at the front. ‘I could only buy E-type roadster A-pillars,’ he says. ‘I had the original brackets in that ruined roof so I could copy them in new steel and turn roadster parts into something suitable for a fixed-head coupé.’ It still left a great deal of work to do. Adam worked methodically from one area of the sill and floor to the next, bracing what was there before cutting out the rotten steel. His determination to keep whatever he could use was not just about the integrity of the restoration; there was a practical side too. ‘A new cowl panel is £1000… if the old one can be saved, let’s save it! I unpicked the securing welds then removed it, repaired it and straightened the bulkhead while it was off.’
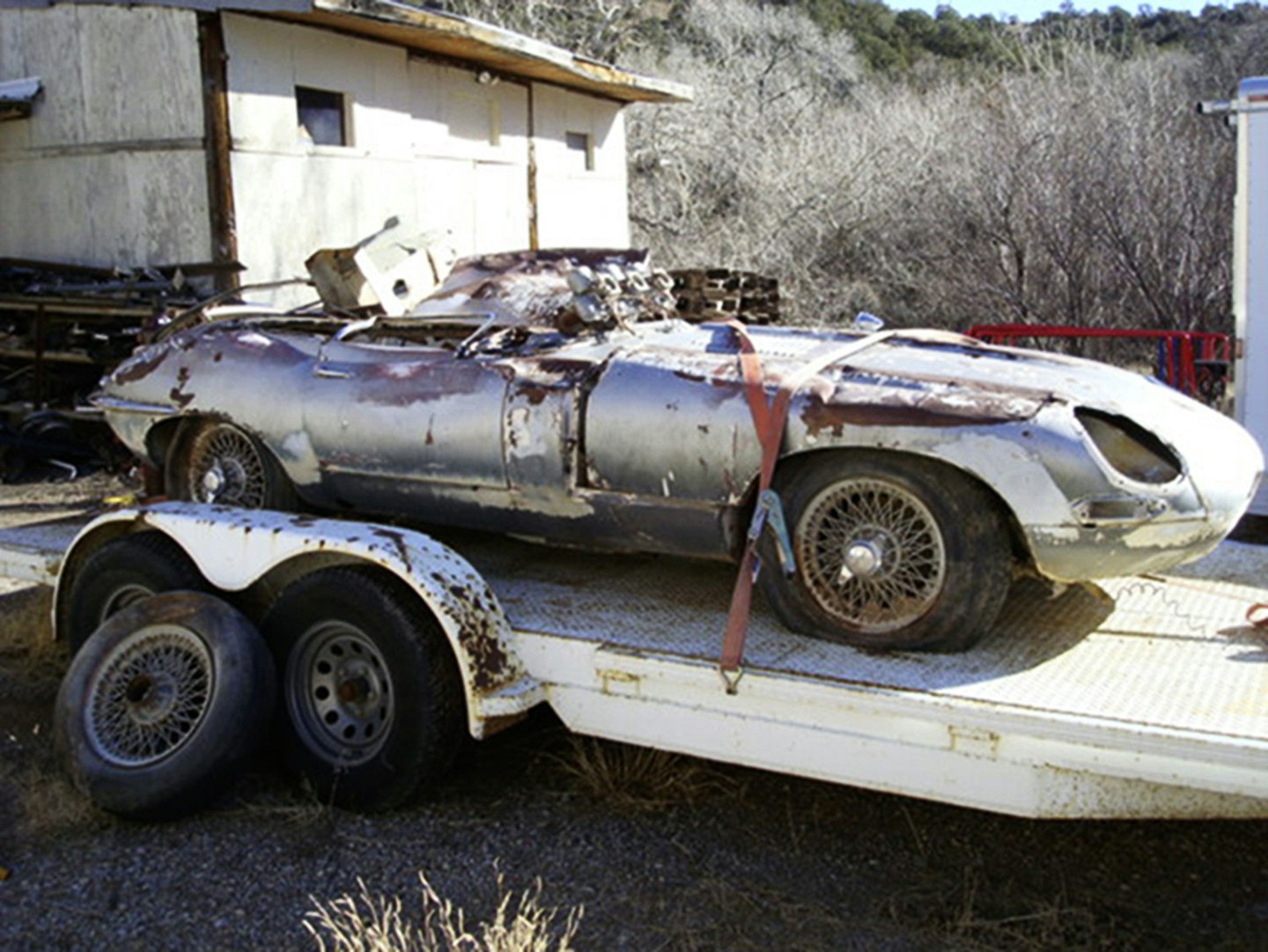
Lateral thinking
‘The boot floor was too riddled with pinholes to re-use.’ says Adam. ‘I let in a new section made by the Hutson Motor Company.’ He then began knocking out the extensive dents to the right-side rear wing, using a hammer and dolly to drift the bent panel back towards its original contours. At the same time, he addressed the nearside’s bullet wounds by tapping the split points flat from inside, touching them in with a welder and grinding them back.
‘As well as straightening the bit you can see I had to sort out a lot of rust in the inner wheelarches,’ he says. ‘With that done, it was time to move on to the engine frames.’
It’s such a critical area that the only safe solution was to buy a pair of new ones from E-type Fabs in Darlington. ‘They’re stiffer than the originals but look identical and fit really well,’ says Adam. This left one of the biggest decisions of all – what to do about the bonnet. It’d been extensively damaged; crushed as well as twisted. Anything can be fixed – given time – but Richard stepped in with another solution, finding an aluminium bonnet in Poland. ‘At the time, it was the only place supplying it,’ he says. But it wasn’t perfect.
‘I think it had been made by two different people and welded together down the middle,’ says Adam. ‘I had to re-work the headlamp areas because the captive nuts were in the wrong place, as were the indicator holes and the bumper mounts. I needed to fold the flanges at the rear and at the bottom too.’
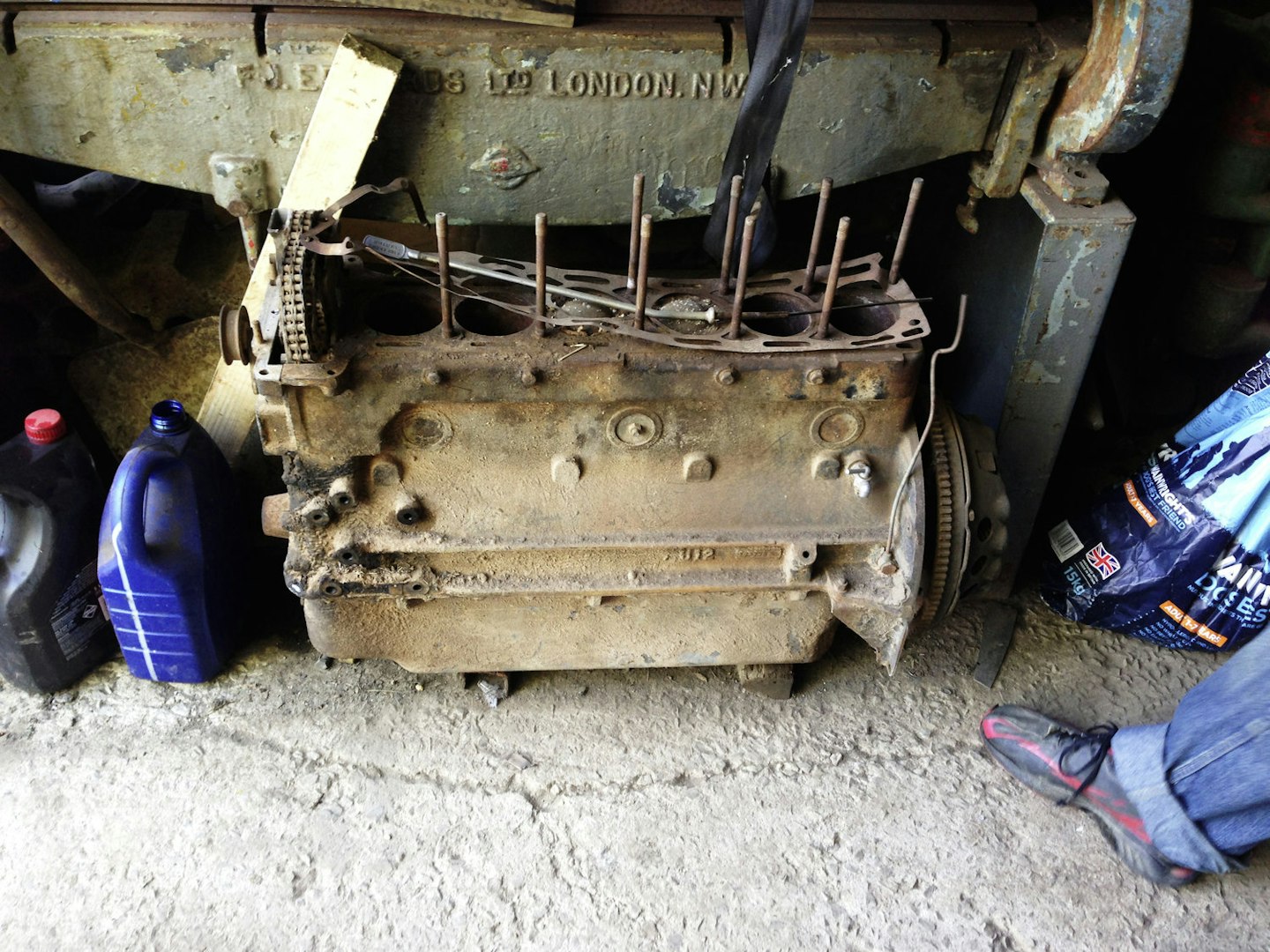
A break from the metal-bashing
While the seemingly endless battle with the bodyshell continued, the engine was also being revived. Adam removed and stripped it – or at least he tried to.
‘The cylinder head had been removed years before, and with the red dust from the desert in the bores combining with moisture, every piston was rusted solid. I removed the crankshaft and then we had to sacrifice the con-rods to push out the pistons from below with a 40-ton press at the local machine shop.’ The team at the machine shop also took care of boring out the damage to the cylinder walls.
‘It needed to go 0.040in oversize,’ says Adam. ‘With new pistons and con-rods required, I was relieved the crankshaft survived, albeit with a grind and polish.’
With the bottom end sorted, attention turned to the cylinder head. ‘The waterways were corroded,’ says Adam. ‘The machine shop welded in new metal and skimmed the mating face. They also fitted new valves, guides and springs. I replaced the corroded camshafts with new items.’
New timing gears and chains also seemed a wise investment, as did a program of upgrades including a Rob Beere high-flow oil pump and a lightened flywheel from the same supplier. What of those carburettors, dangling out of the boot on their furred-up manifold?
‘We could save two of them,’ says Adam. ‘The third was so corroded we had to buy a new body, but I rebuilt all three so you’d never know the difference.’
Adam also rebuilt the car’s Moss gearbox, one of the few jobs that seemed straightforward at the time. ‘There were no major issues,’ he says. ‘At least, not then. Those came later.’
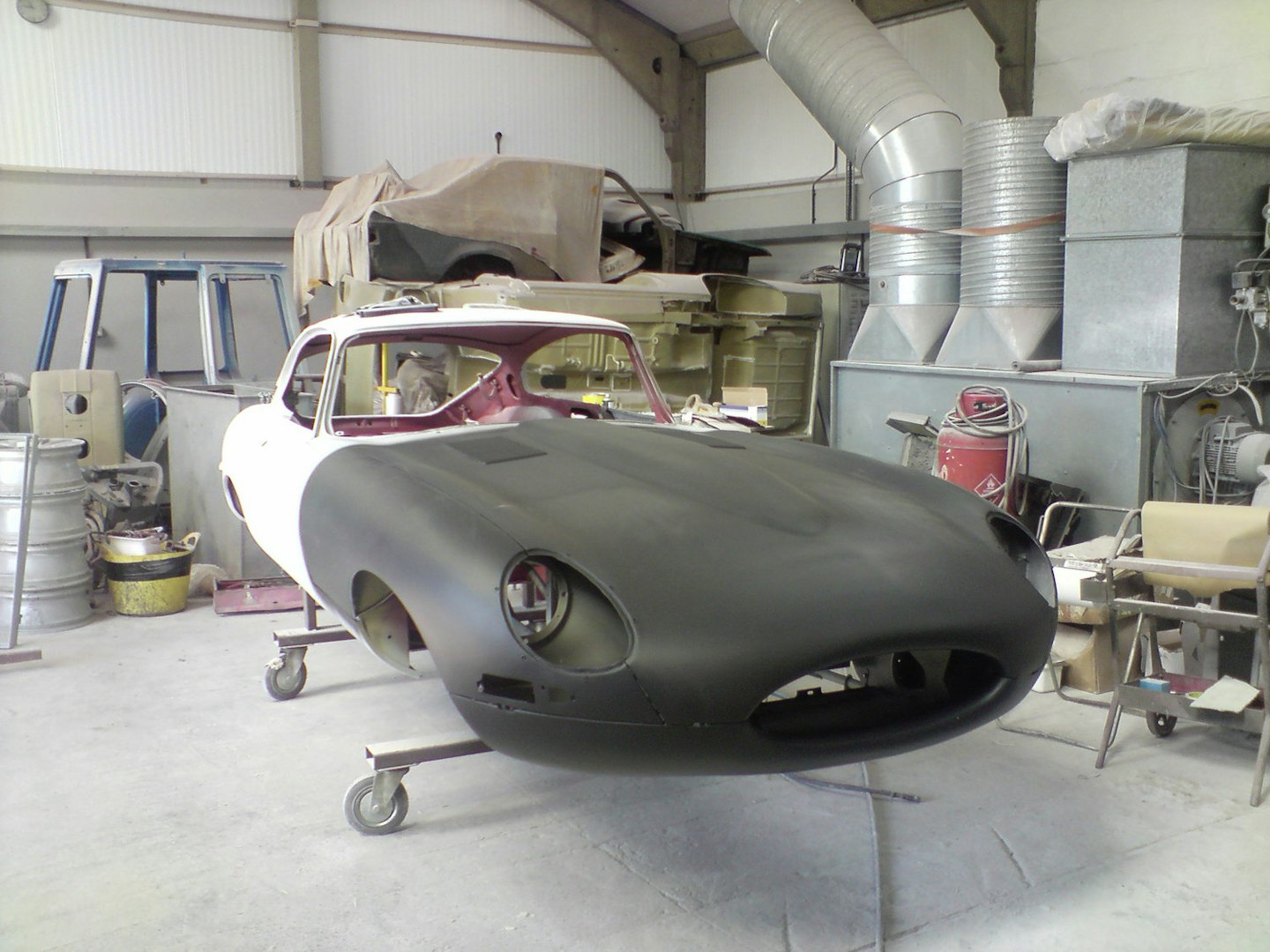
Major milestone
‘The repairs to the bodyshell seemed to go on for a long, long time,’ says Adam. ‘You keep plugging away and sometimes feel like you’re getting nowhere, then one day later you’ve finished.’
The shell was finally as stable as it could be – every panel had been fixed, the roof and pillars completed and the door skins replaced after the frames had been straightened and repaired. Adam was able to move the body tub to JC Shot Blasting in Carmarthen for surface preparation.
‘Ceri Richards at JC did it very gently so even thin panels like the roof were at no risk of deforming,’ says Adam. ‘Ceri is the painter too, so he was able to control every part of the process from keying the bare metal to laying on sealers, primers and eventually top coat.’
The repairs to the shell had taken Adam from February 2013, when the car arrived, to March 2014. During the work, he’d taken a break to strip and deliver the engine to the machine shop, who returned the parts in April 2014. Around this time, the preparation for the paintwork began, with Ceri Richards finally returning the re-finished car in the first days of 2015.
Through the second half of 2014, then, Adam had plenty of time to revive the running gear. Here, as in other areas, Richard Feather’s philosophy for the build was about making it a driver’s car to be enjoyed while touring, mostly on the continent. ‘That’s why I was happy to leave it with left-hand drive,’ he says.
Richard bought a different crown wheel and pinion to lengthen the back axle ratio from 3.54 to 3.31 for more relaxed touring. Adam also fitted adjustable-bias Coopercraft brakes front and rear. He assessed the wheels and hubs that came with the car but felt such safety-critical items could not be re-used, so he sourced four new hubs while Richard bought a set of 6J wire wheels from MWS in Slough.
‘We could re-use the original wishbones but fitted uprated torsion bars,’ says Adam. ‘I also added an adjustable reaction plate. It really simplifies the process of setting the ride height.’ A further aid to speedy set-up was the fitment of adjustable camber bars instead of shims to set the camber of the front wheels. With all bearings and bushes renewed and a great deal of blasting, priming and re-painting, the running gear was ready to meet the painted bodyshell.
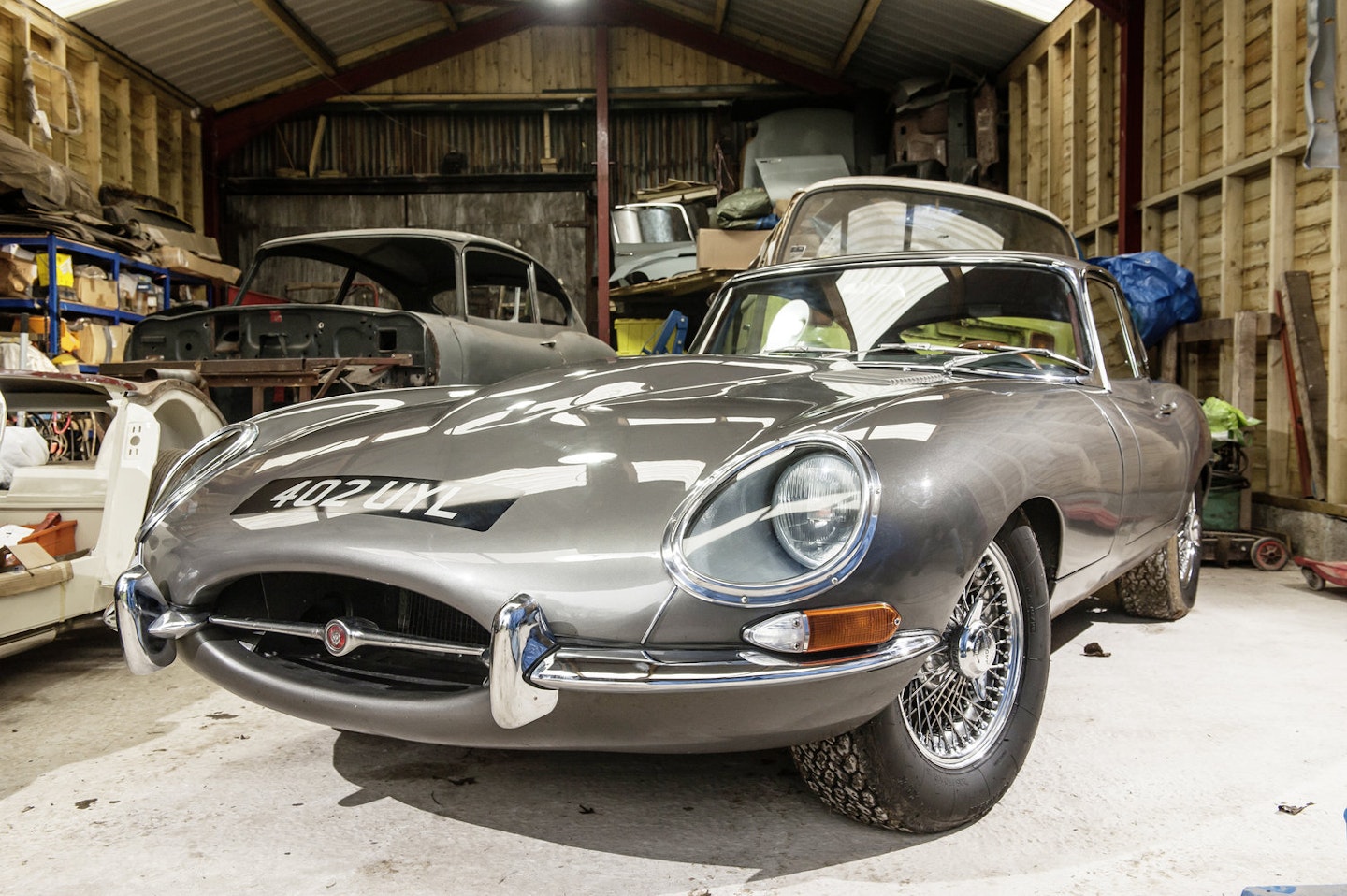
A fast finish – at first
Adam tore into the build-up of the car with impressive speed. After taking delivery of the painted bodyshell in January 2015, the assembly work was completed by April, including the added features for an improved driving experience.
‘I knew it would need aircon,’ says Richard. ‘It’s vital for comfortable use in the summer when driving in Southern Europe. Adam was able to find a home for it in a box in the passenger footwell and he turned the heater switch into an on/off control, so now I just use the sliders for hot and cold air.’
Next came electric power steering, handy for other Feather family drivers without Richard’s shoulder muscles. This kit, supplied once again by E-type Fabs, can be set to add heft as speed increases, so it’s never floaty-light. Adam and Richard agreed that halogen headlamps would make a big difference to visibility for night driving, which just left in-car entertainment. ‘The original radio fascia is a dummy,’ says Richard. ‘Instead, you can stream music from your phone to a Bluetooth receiver hidden in the passenger footwell.’
Replacing the original loom meant Adam had a chance to wire in all these fresh accessories – plus the hazard light circuit from an S2 E-type – leaving only the trim to do before the car was finished. Says Richard, ‘I thought it was so close by April 2015 that if I just got the front seats done, we could MoT it and start the shakedown process.’ So Carl Stanley of Stanley Trimming in Somerset finished the seats and sent them to Adam to fit. By the following month, the car was road legal. Richard promptly set off on the Mendip Tour – a classic rally – and then crossed the Channel for a first trip to France, all in a largely un-trimmed car.
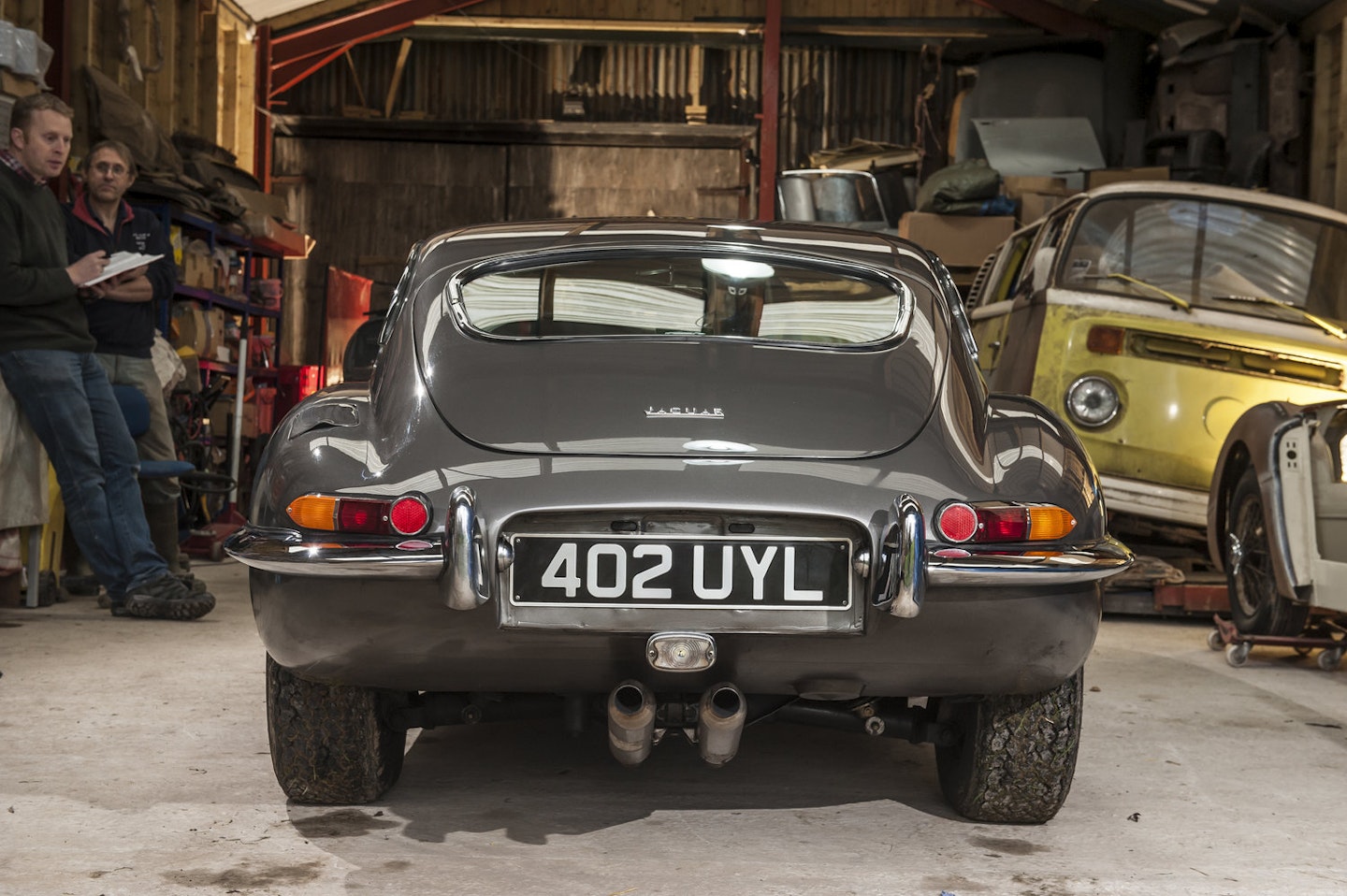
De-bugging and perfecting
‘It actually went really well,’ says Richard. ‘There were a few issues, like discovering fuel slopping around in the car after the old tank, sealed by another company, sprang a terrible leak. I bailed it out and carried on.’
Needless to say, a new alloy tank soon replaced the original. By July, with the French adventure over, the car was returned to Stanley Trimming to be finished off. That took until the winter, so it wasn’t until the following year that the shakedown process could continue. A lengthy run in the fully leather-lined Jaguar took Richard through France and into Italy, where the final phase of ‘development’ began…
‘The gearbox input shaft bearing melted,’ says Richard. ‘The recovery driver who collected us had also rescued Daniel Craig and his Aston Martin from the same place, so we felt in good company.’
‘The Moss gearboxes aren’t as sturdy as the modern equivalents,’ says Adam. ‘Richard preferred a five-speed anyway so I fitted one from E-type Fabs.’
One final tweak gave the car a unique touch. Says Richard, ‘The speedometer’s face is a custom job, showing both km/h and mph. It looks factory but isn’t. It makes things easier when driving in Europe.’
Richard’s restoration has led in an unexpected direction. Since the E-type was finished, Adam has restored E-types for other customers but also two MGAs and a Citroën 2CV for Richard. These now form part of his classic rental fleet in the South of France, while the E-type has covered more than 8000 miles already. What started as a bold, impassioned mouse-click one New Year’s Eve has grown into a sustained working relationship and a business of its own.
Ever thought a restoration is just too hard, too much to bother with? Maybe Richard and Adam’s next project together could involve motivational speaking.
Thanks to Provence Classics (provenceclassics.com), ATB Restorations (atbrestorations.co.uk, 07754 712737)